FINAL BUILD no 302 heads
The only way a block can be square decked is if the mains are attended to first. Regardless of fixture manufacturer, they all use the cam bore centerline, and the crank bore centerline, to set up the deck height. So, you can chuck a block up on any milling machine with a BHJ style fixture, but if the mains are not corrected (and we all know how good factory machining is in terms of accuracy) the deck may be flat, but if wont be parallel with the crank centerline. Similarly, the same equipment bores the holes. So while the block is in the fixture, all 8 holes are bored exactly spaced properly, and exactly 90° to the deck and crank centerlines. Like BJR said. You either do it all, and do it right, or you dont, and IMO anyway, waste money. Old school horizontal millers cannot square deck a block. They dont have the capability to cut the surface as flat in terms of right to left as opposed to front to back, or with the right finish for modern MLS gaskets either. If you look at the milling equipment, and it has a round disc with cutters evenly spaced around it, and a large arm that the motor and wheel are mounted to coming out of the large flat table, walk away. It's fine for rebuilding flat heads, and stovebolts, and farm equipment. It has no real value in a modern performance automotive machine shop. In fact, the shop that just closed trhew one out because no-one wanted it. When I rebuild an engine, any engine, there are certain things that get done regardless of output: the usual cleaning/magging, then (in this order) align hone the mains, bore, square deck to set my piston's installed compression height. In the shop I recently switched to, that's all done on a CNC Rottler F-65A. Attached is a pic of the fixture in use on the manual version F-65M where I had been going. Not the cutter is sinlge, the round disc is a shield. The spindle speed and feed rates can be set +/- 1rpm, from 0 to 3000+ as needed. That's where the surface finish for Cometics and MLS gaskets come from. Old millers cannot control the speed well enough, and because the flat disk has to be angled slightly so only one side cuts as it crossees the surtface. So depending on diameter, the center of the sweep will be cut slightly deeper than the edges. (think about the ride at county fairs where teh people stand up, and it spins, then tilts. The cutting hed is tilted the same way. When you shoot for demensions for quench of exactly .035 and the outside of the deck is flat, the center (between the cylinders) is .002 deeper, that dip can be a pain to account for and a gasket sealing issue. That sounds anal. But things like this are the difference between a performance build, and a repair back to stock factory shape from wear.
Sorry for the ramble attempt at clarifying. The reason the "old guys" say dont bother, is we've spent the money, and found out that for what you are intending, you dont have to spend or make that effort. You can always say "but I want to to be right". But sometimes, factory is good enough. Your's is one of those cases. And truthfully, I've had less trouble from junkyard jewel spray cam rebuilds with a cam, than some top dollar build ups. Spend if you want. You're headstrong and will do what you want. Just try to understand the reasoning behind the advice.
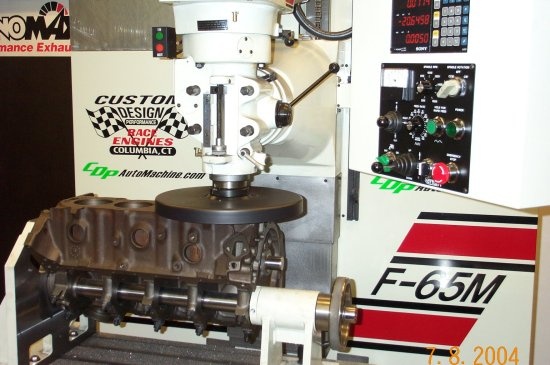