How thick of metal for frame connectors
update, just finished one side. I'm $20 bucks into it, and that includes tax! 2 pieces of scrap 1.5X3 14G rectangle @ .99 a lb (9# each @ 48 inches, didnt have 1X3 in stock) cut them 2 X 44" total, cut the top out at about 36 inches so you have an 8" opening. cut that piece to use as the butt plate on the front, weld 2X5 but plate. Test fit on raised car (4 jackstands, in pairs front and back on concrete slab to make sure the frame is completely square)-driver side- and make a notch for the E-brake cable as that is where it wants to sit naturally using 1.5. 1 may sit right under it if you lip it under the cross brace. Use a jack to snug it up, then use a hammer to bend the butt plate flanges flat against the cross member, it bends a little forward outboard or I had a crooked cut? Anyway, once it is flush, tack front and rear, check out and then lay bead around the butt plate and rear channel outboard side. Take hammer to inside and beat inside flush with frame rail as it seems to reduce in width. Lay bead when flush. Repeat on other side! 14G slides over rear channel perfectly, thicker will not clear without working metal wider. Good afternoon project and well worth it. Probably do it in about an hour after yoiu get the materials if you have a chop saw and a cut-off wheel. My welds are pathetic but they will get a good slather of seam sealer and black paint. Overhead welding is fun! :-(
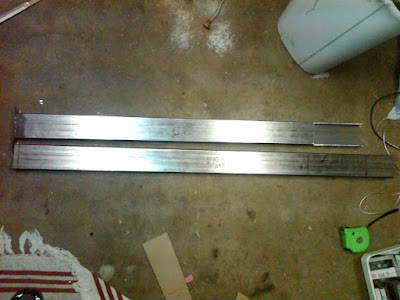
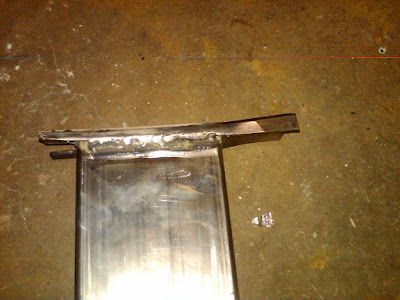
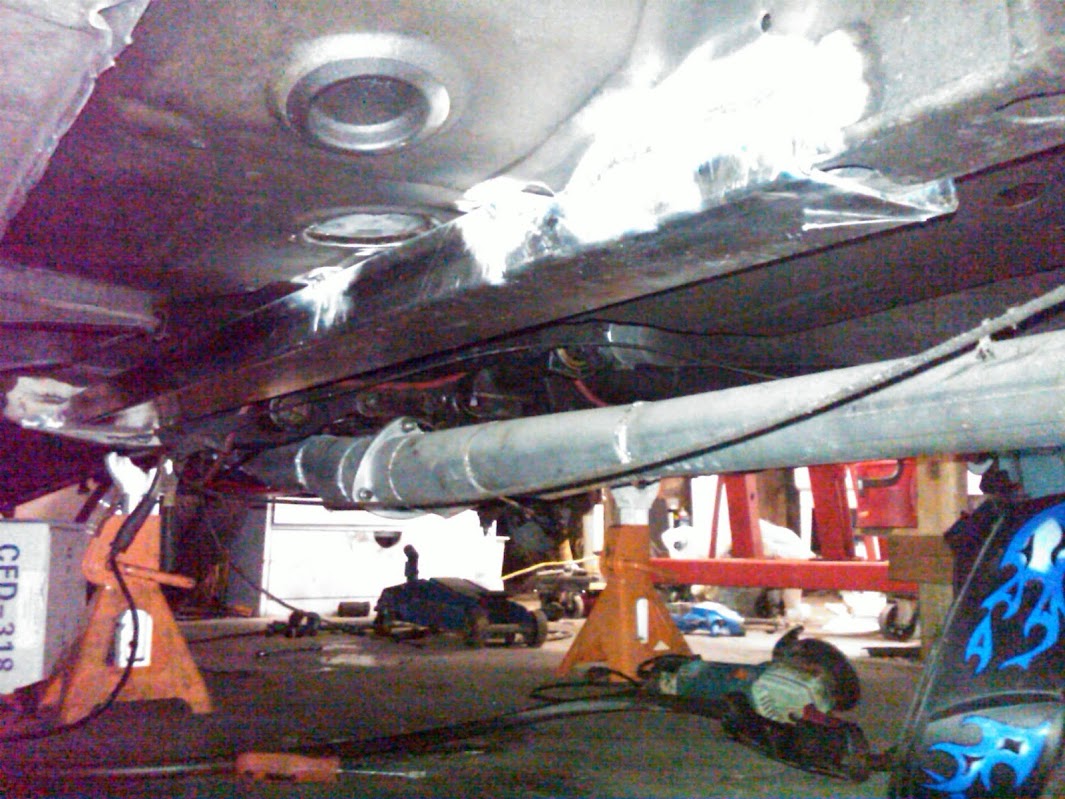