Milling for compression
If losing .100 of thread engagement causes the head bolt to fail Mopar did a really poor job the their R&D of the slant 6.
.1" of thread engagement is not lost. I wasn't even talking about losing any thread engagement. What I wrote was that the OP would have to remove
.2" off the bolt threads so they don't bottom out "if" he removes .1" off the block and .1" off the heads. If you take .2 (total) off the heads/block then the head bolts should be .2" too long. The other point that I was making is that you have to be sure that there are at least 2/3 threads left unused (above the block). Thread theory (taken from "engineerdog" website) states:
""Bolts actually stretch very slightly when force is applied, which causes the loading on each thread to be different. Because of this stretch, when you apply a tensile load on a threaded fastener the first thread at the point of connection sees the highest percentage of the load. The load on each successive thread decreases from there, as seen in the table below.
Additional threads beyond the sixth will not further distribute the load and will not make the connection any stronger.
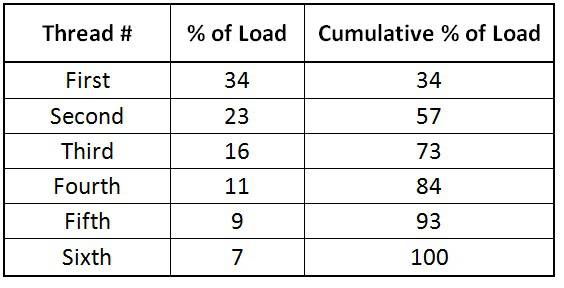
""
This is the reason that all head bolts have about 3 or more threads still visible (if you could see through the head) once they are properly torqued. If you only have "one" thread showing above the block surface then that one thread ends up taking 100 percent of the load. This would be a point of potential failure since the shank (un-threaded portion of the bolt) is stronger than the threaded portion). As you can see from the chart above, the few threads that are left above the block as like a spring to absorb load (torque).
I was trying to warn the OP that if he removes .2" off the bolts he should try and ensure that there are at least 3/4 threads still left protruding once the head is torqued.
I'm not making this stuff up.
Treblig