Structural Foam for chassis stiffening
lol,,,did anyone even look at the SAE papers I posted links to? They address a lot of the speculation & guessing posts.
- None of the vehicles tested by Chrysler, GM or Mazda were initially "designed" with structural foam but all showed surprising and positive results.
- Foam density is critical. 8-24lb/ft3 densities were tested. DOE showed that 8lb/ft3 foam to be the most efficient in terms of weight vs % improvement Hardware store "Great stuff" isn't even close at ~0.5lb/ft3. 3M 8458, Rigid Pillar foam is around 20-30lb/ft3 irrc. BWM's foam(TEROCORE® 1015AA)is ~30lb/ft3
- Proper surface adhesion is a valid concern. The Mazda paper actually tested it but it appears that what they used and how they tested it may have elevated the importance of foams adhesive strength. The BMW foam and 3M's 8458 is intended for well used vehicles but obviously not rusty 40 year old A-bodies.
- As shown in all 3 papers, the focus wasn't on fully filled larger cavities but the JOINTS where one reinforcement met another that proved most important. So I'm thinking it's not worthwhile to fill the entire cavity between the inner and outer rocker panel but the JOINTS where that structure ties into the Cowl, A,B,C-pillars, ect. With that in mind, with the proper fill and density, smaller volume of foam will mechanically locks into the "joints" as it expands into the nooks and crannies, thus reducing the dependence on surface adhesion strength.
- Testing isn't terribly complicated especially since its a comparative, % improvement result. XV & US Car Tool showed similar test fixtures.
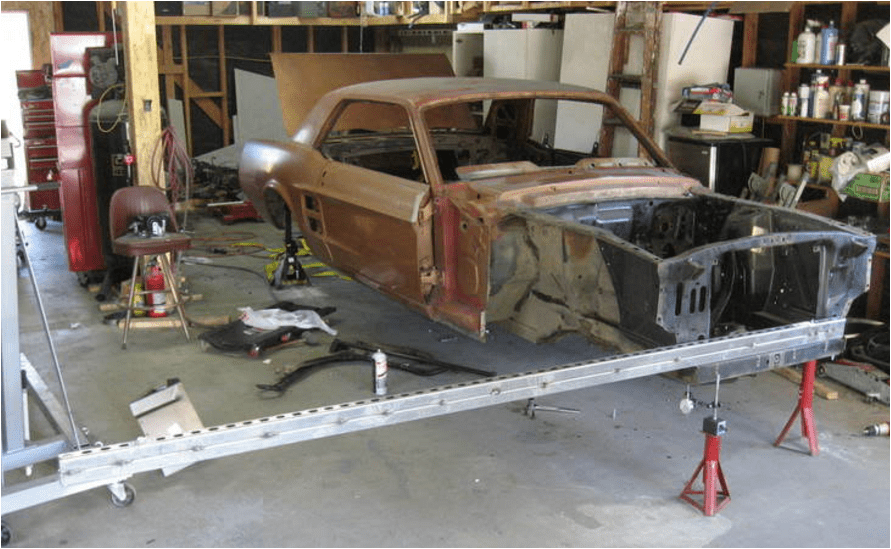