67 barracuda notchback restoration
My car came with a leece neville made Vspeed wiper motor. Both my old chargers only had low and high 2 speed wipers. I never heard of a variable speed wiper setup until this car. Its essentially a switch with a low speed detent to get the party started, then you can smoothly rotate the knob like a rheostat all the way to high speed. I guess this was before they figured out delay action wipers. Well i took the motor apart to rebuild. I find out you cant get squat parts wise for this motor.
So i go back to the boneyard to hunt for a prestolite Vspeed motor or 2. As i pull in i notice a sign that now makes me more cautious when walking around the cars and getting parts. Salvage yard owner tells me prob $10 each. Go see what you can find. Back to the half stripped 67 in the boneyard, get the first motor, and crank arm, then get motor number 2 off a 68 fury. I go up to the salvage yard checkout counter with these deplorable looking things that have been sun baked and rained on prob over 10 years, and the owner Gene tells me oh hell those things look so bad i cant charge you for em. Just take em they are free. So i thank the man and head home with my new rusty treasures.
I get 2 boxes and take each motor apart one at a time and put em each in seperate boxes. Then i start to round up the best pieces from each motor. I decided to use the 67 as its date coded for 67. Only difference i found between the 2 was the 68 the motor can and armature are a little longer. Everything else looked the same. Both crank arm drive gears were shot, and rubber mounting gaskets both shot. Got those off ebay, motor gear housing went into the sand blaster, motor can or drum went out to get cadmium plated. I put the armature on a drill press and using fine sandpaper on a flat piece of wood i smoothed out the grooving in the commutator. Then smoothed up the mating surfaces of the motor brushes
I rewrapped all the windings with new winding paper and fiberglass tape to replace the cloth tape. The wires coming out of the windings use color coded fiberglass cloth tubing. Enough of it was unfaded inside the motor that i could figure it out. I decided to use shrink tubing in the colors they used. I was able to also get short stainless steel countersunk screws that hold the iron motor poles in place from my local fastenal.
Everything went back together using areroshell 22 synthetic grease. This stuff does not dry out and maintains consistency in extreme hot or cold temps. Wired up the harness with all new color coded wires crimped to new spades and plugged into connector. Fabricated new ground strap from brass sheet i purchased at hobby lobby. Bench testing will only put the motor in low speed, high speed, and reverse/park. Motor worked perfectly. I am prob into it for about $150 or so. Compared to $350 up for one already rebuilt plus i know how its put together and can easily fix it if need be.
I have one more of these to build up fo the 69 notch i'm saving for my son. I have the 68 motor in pieces, and an assembled 69 motor i got from another fabo member, plus the shrunk tubing, fiberglass tape, winding paper, copper wire and other odds and ends all packed up in a box until we are ready to rebuild onefor his car.
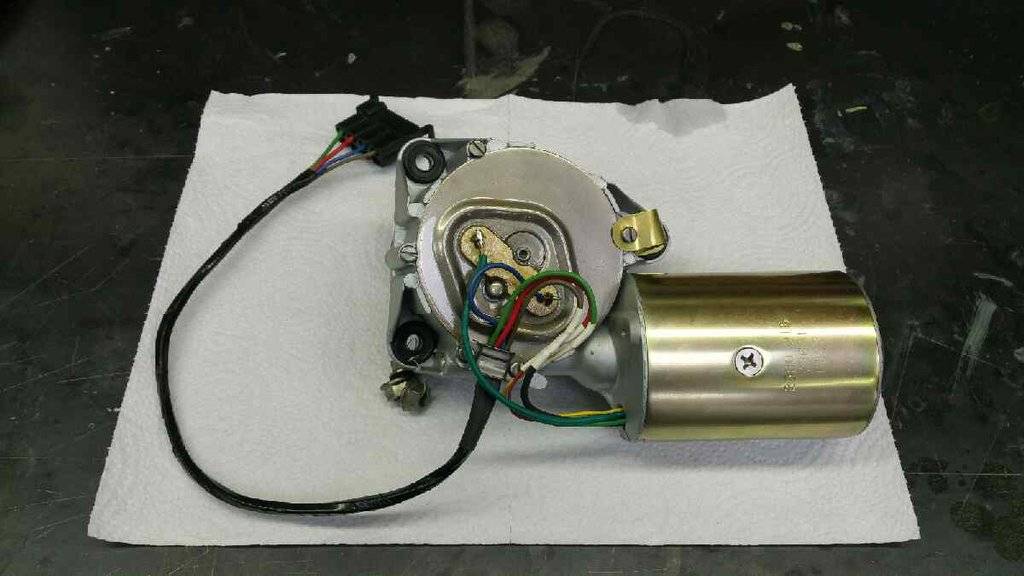