Need Advice on Machining the Intake Surface of the Head (gasket crush)
Got my open chamber heads (3418915B's) back from the machine shop. They removed 0.012 from the deck side to reduce the chamber size to adjust compression. They did not take any material off the intake side of the head. I've performed a trial fit of the intake manifold / heads on the motor with the head gaskets in place. I fabricated some washers the approximate thickness of the Felpro intake gasket (0.055 / 0.060) to place between the head and intake, and used clay between the head / intake to measure theoretical gasket compression. The head bolts were just snugged up.
These photos show the actual thickness of the clay. The measurements show that the desired compression is reversed, i.e., the compression is greater at the top of the port, less on the bottom of the port. The compression also varies front vs rear. I'm using the guidelines in this article,
http://www.hughesengines.com/Upload/TechArticles/INTAKE_MANIFOLD_SEALINGJULY2015.pdf, i.e., for example, add the clearances at the top of the port for the front positions, do the same for the bottom of the port, you want 0.006 / 0.008 more clearance at the top of the port for proper sealing.
Using my measurements,
Front position (top of port): 0.050 + 0.050 = 0.100
Front position (bottom of port): 0.053 + 0.065 = 0.118
So there is 0.018 more compression at the top of the port.
The rear positions:
Rear (top of port): 0.051 + 0.056 = 0.107
Rear (bottom of port): 0.055 + 0.060 = 0.115
0.008 more compression at the top of the port.
The machine shop has the heads and they will come up with a proposed solution.
Just thought I'd run this by the machinist / shop owners on FABO to get their input.
Thanks in advance for any inputs.
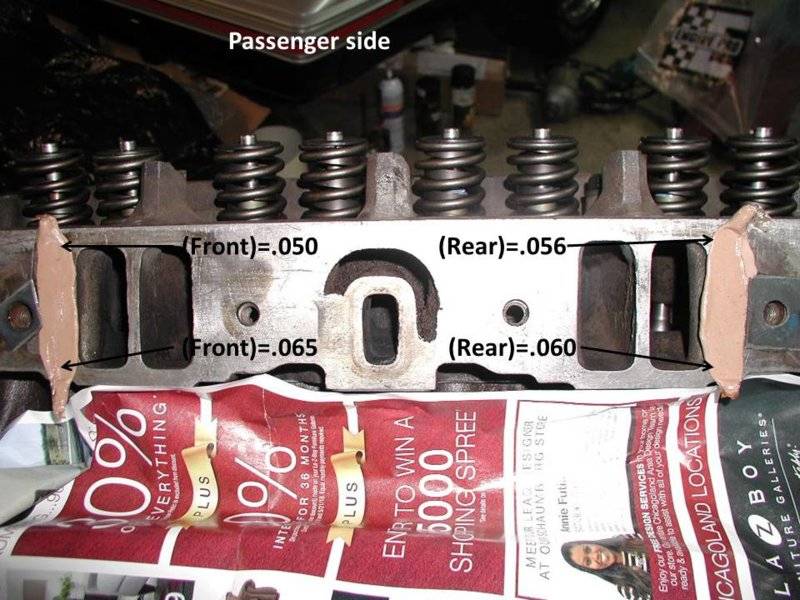