KB's in a 318 with No Re-balance
Next problem is how to secure the sleeve inside the pin for good. 2 candidates seemed to be good. (But there may be others; I’m open to suggestions.)
· Tack welding at the end
· Using sleeve retainer compound, like used for cylinder liners, valve guides, small motor winding on their shafts, bearings in housings, etc.
The welding has not been tried. Some effort has to be made to do proper preheats and cool downs, to deal with the different steels: mild steel in the sleeve, and tool steel in the KB pins. The weld has to be recessed so as to not interfere with the pin locks. And, it has to be done so as to not distort the pin’s diameter, as that has to be controlled to well under .001”.
So the sleeve retaining compound has been tried. The .001-.003” clearance is very good for the Loctite 640 and Permatex 64000 Hi Temp Sleeve Retainer compounds; they will fill up to .007” diametrical difference. After a quick hone of the inside of the pin to clean it up, and multiple cleanings of the sleeve and pin, the retaining compound flowed on easily and seemed to wick in and fill very well when the sleeve was inserted with a twisting motion.
The pin was set horizontal during curing, and cure was at room temp for 24 hours per mfr’s instructions. Afterwards, the pin was solidly held in place. To test, a 360 block was suspended just from the sleeve while the pin was clamped in wood blocks. After 2 hours, the load was removed, and the end clearance of the sleeve to the pin was re-checked with a depth micrometer; it was still as before the load was applied, at .0113” so no creepage occurred with this load.
To give you an idea of the ultimate strength in this configuration. I went through the MIL test specs for these compounds in detail and confirmed what I had read elsewhere, that the total shear strength is the bond area times the compound strength in psi. Since this is rated at 3000 psi at room temp, and the bond area here is just over 6 square inches, that is 18,000 lbs….! So even if you got 1/10th of that number, you would be good for this application as there is no actual load on the sleeve; it just has to be kept from moving. This particular long cylindrical configuration is very good for this retaining compound.
How this sleeve retainer compound will work over temperature is a very good question. It is rated to work from -65F to +400 F. Per the Loctite Tech Data Sheet, if held at 350F for over 500 hours, the strength will drop to about 50%. The product’s strength is not effected by hot oil. And the disassembly instructions on the Permatex product package reads: “To disassemble parts, weaken cured Sleeve Retainer by heating above 500F and then use pullers to separate parts.”
So things seem pretty good over engine operating temperatures.
Is there a hidden problem with the weight or the sleeve retainer compound? Well, if I knew, it wouldn’t be hidden LOL. But as always, ideas are welcomed.
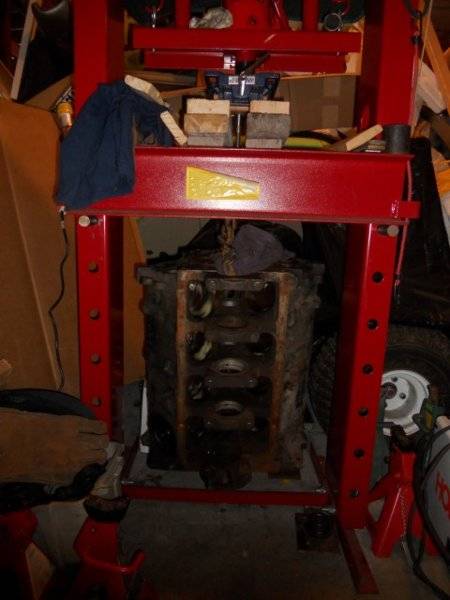