Flexing a Flex Plate?
Send the converter back. That converter will not spin concentric with the notched flex plate for a 360. The flex torsion of the bolts pulling the plate back against the converter will not be even. Just looking at the converter assembly you can see the thing is not that impressive. It looks like a converter shop made it using a factory converter cut down to create a higher stall. Right here is a good example of cutting converter cost and the problems you run into. ATI anti balloon converter was $2000 . Worth every penny spent. There are cheaper converters better than the one you have. I have seen my motor go over 9000 Rpm's . Smooth as a well balance electric motor. "Neal Chance" converter would be my first choice but my 65 year old feet are not worth that much
A good example is take an old electric motor and install a balanced pulley and run it. Then drill a small hole in the pulley and run it. Now just thing what that is doing to the motor and bearings with the harmonics of the out of balancing that you are creating. Send the converter back spend a little more money on one that fits properly. I myself would never use a spacer or shim on those bolts. Did you ever see a what a piece of clutch plate steel does to the floor of a car with guys running aluminum bells. I have seen them go through dashes and windshields. I would hate to see what one of those shims would do to your toes.
Picture one of those spacers going through your foot. You could just wear those big Herman Munster shoes. Or put an extension on the throttle pedal. LOL.
There is a quick fix for everything. Do not apply one here. If you were running a solid flex plate as pictured below without the notch you may get away with pulling it tight safely. But what you have to remember it is called a flex plate for a reason.
Another thing where are the weights on that 360 converter that calls for that notched 360 flex plate. I don't see them. Unless they are hidden in the pictures
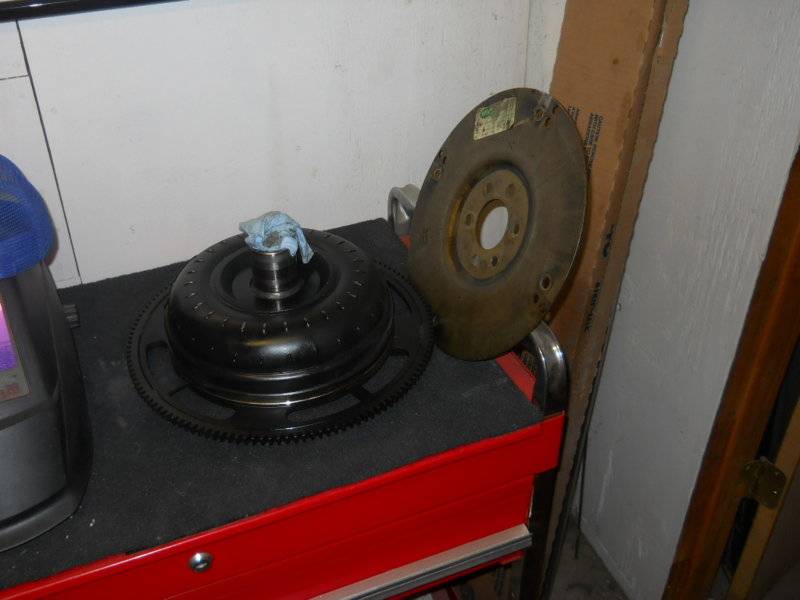