Where did the spot welds go
Are you changing out the main floor pan? If so it's a *****. I have done 2 of these. Use a cutoff wheel on the "floor pan side" to cut loose the floor where it meets the firewall leaving a flat spot welded strip attached to the firewall sheetmetal. After you get the rest of the floor out of the way you can assess this thing from inside the car. Use a sharpened putty knife with a good handle and hammer it inbetween the strip of floor pan flange that's left and the firewall this will pucker up the first weld you will find.
Use a ball rotary file on an inline air grinder and carefully grind all around the perimeter of the weld to weaken it, then cut thru it with the putty knife and hammer and on to the next one. When you get to the left and right corners it will be harder to access the lip to drill it. You dont want to drill the spot welds on the sides of the metal you intend to keep if you can help it. In my pic you can see no holes drilled on the firewall side, and how it gets tight at the framerail area. It took several hours with a ball rotary file, hammer and putty knife to carefully get the strip of firewall metal out. When I am changing out a floor pan I only keep in one piece. The critical stuff that I have to transfer to the new pan like console shifter mounts etc. This way I have a way to measure to transfer it all. Once I got the dimensions off the console, and took pix, I scrapped the tunnel.
The rest of the pan use a cut off wheel to get it out of the way in smaller pieces being mindful to not cut into the frame. After that you have strips of metal covering crossmembers and outboard seat brackets. You can sit inside on a small stool and peel the rest out with the method i described. Its messy sucky work, but the results are well worth it.
Notice in pic #2 the inline air grinder to the right of me, and the floor strips peeled up with ground in circular rings from the ball rotary file on grinder. Wear rubber gloves and safety glasses because of the metal splinters it gives off. Do not use a 90° angle grinder with a rotary file it will kick back at you like a rented mule. Slowly grind around the perimeter of the spot weld on the side you want to remove. Do not grind the center of the weld as the metal is thinner from the 2 pieces being squeezed together. When you see a puff of brown, or notice a thin brown rust line that's separating the 2 pieces of metal then that's deep enough. Is this time consuming? You bet it is !! Will it help prevent you from drilling too far and damaging the metal you need to keep? Absolutely. It took me roughly 10 hours to get to where the car looked in the last pic, but I have done enough body parts replacements, not just the 2 barracudas. If your swapping the whole pan, give yourself a few days. And go slowly as to not damage the pieces your trying to keep.
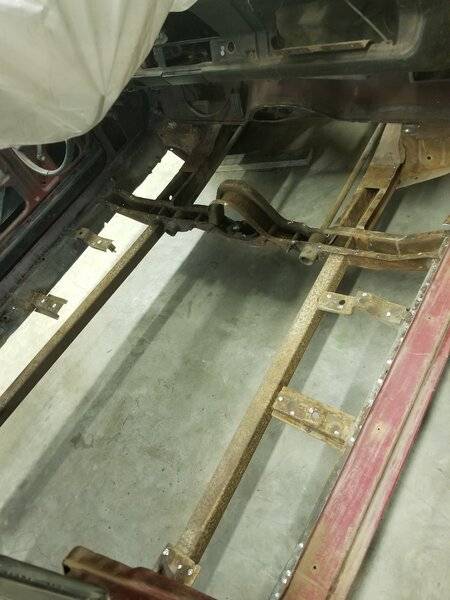