Project Crusty Biscuit (65 Plymouth Valiant)
Sometimes you have to re-do things. I recently installed the hood on the car and noticed a massive 1/2” height difference between the hood and the cowl.
The first mistake I made was using the crappy 22 ga Home Depot sheet metal foil to patch the cowl vent. 2nd, I left the sheet metal flat when I welded it on even though there is an obvious curve in the panel. I have since learned the value of shaping and forming any metal patch panels even if the curvature is only slight and also taking the time to get it to fit perfectly without having to fenagle the piece around as you lay tacs.
I also did the patch work before the cowl was installed on the car and didn’t think to match up the gap between the it and the hood.
Here’s a pic of the gap I’m speaking of. Looks like a poor attempt at cowl induction!
Old cut out
I had to use one of my paintless dent removal rods to work the edge up to meet level with the hood.
I cut a new piece from some nice proper 18Ga sheet, took several hours to trim and form, and ended up with this fitment!
Here’s welded in:
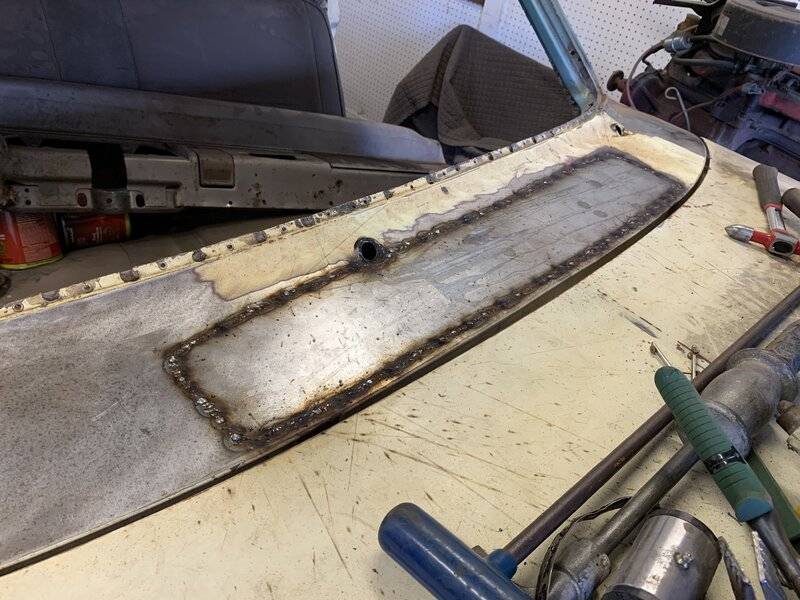
Final after grinding the welds and going over with 80 grit on the orbital sander:
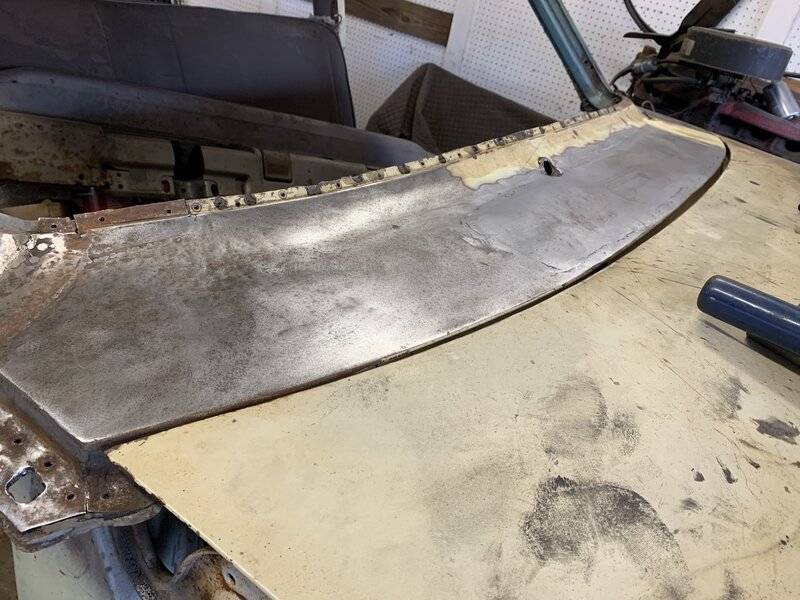