Pushrods And Trick Flow Heads
That is a MASSIVE correction right there. How many guys are running the same stuff uncorrected and wondering why their valve train is pissed off.
Right! The motor was initially dyno'd and run for several thousand miles with insufficient/incorrect spring installed height on a pretty healthy hydraulic roller. This resulted in all the needle bearings in just the exhaust rocker arms being disintegrated and dropped into the motor as metal dust and bits of the retaining cage. I spotted it while doing routine inspection/maintenance. All the intake rocker arms were fine still. Perplexing as h*ll.
I reached out to Dwayne Porter, who solved the mystery. My intake pushrods were starting to flex like wet spaghetti noodles until they hit the outside of the intake ports a few thousandths away, which dampened them. While the exhaust pushrods were free and clear of contact with the head all the way from the rocker arm to the lifter. Those things must have looked like a string flopping in a strong wind due to the harmonics going on inside my engine at rpm. They were 3/8ths chromemoly steel pushrods too. Dwayne had me send him my dyno sheets, where he spotted the rpm where my springs lost control of the valvetrain at about 5800rpm. The motor dipped about 60hp right there, and then the harmonics really kicked in. I had always shifted at 6500rpm.
Thank God I run a Jomar 100% No-Bypass oil filter, as none of the debris was pumped through my bottom end. All my bearings looked new.
Dwayne replaced all the hard parts in the heads, increased the pushrod clearance, rebuilt them and guided me to an amazing solid roller cam. He also, took the extra time to help me order a set of custom pistons to get my compression ration down from 12 to 1 to a pump gas friendly 10.2 to 1 at the same exact weight as the high compression pistons I removed.
I then contacted Mike at B3 racing, completed his measurement document and he set me up with a geometry correction kit and ordered me a set of custom T&D rocker arms to further optimize my geometry.
I contacted Manton Pushrods and told them what had transpired. They told me to run the stiffest pushrod I could afford to fit. He advised me that weight really does not matter on that side of the rocker arm. I went with their 7/16ths Stage 5 units. While not cheap, they helped with the overall combination of quality head work, proper valvetrain geometry and helped this motor run smoother, quieter and rev easier than any RB I have owned over the last 4 decades. There is a night and day difference in this motor now. It thinks its a small block with the way it revs.
I elaborate here to illustrate the difference and importance of optimizing the valve train set-up instead of just bolting on a set of rocker arms. It truly is the combination, proper machine work and quality parts.
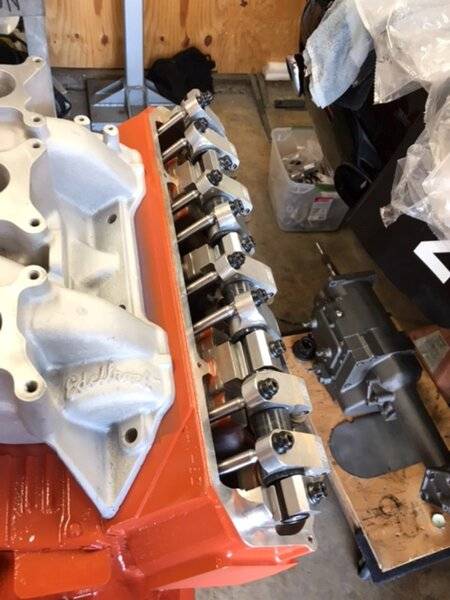