New Tool from Bad Cam
Hey I know this is an old post but I was wondering how this worked out? I'm about to cut grooves in an old cam myself for the same reason.
I cut the grooves in the used cam journals considering I would be turning the camshaft clockwise. I slightly cut the groove a few degrees from perpendicular (90°) to help it cut on the clockwise rotation, and if you needed to back it up it will let go then.
Once the angle cuts were finished I used some 180 grit sand paper to debur the cut at the cam journal surface so it would not be scratching the bearings.
More or less the cut grooves provide a relief area for the thick assembly lube and gray bearing material to fall into as you are rotating it to final fit the bearing to the cam journals.
I used short pieces of high density foam to plug the oil supply holes so bearing debris does not get into them during the fitting, then pull the foam out with a pair of tweezers when done cleaning up.
Threading a 6" bolt into the end of the cam helps give you something to grab onto, and helps to balance the cam evenly as you are pushing it into position.
Also the cam lobes can be sharp and can nick the bearings as you are working. I also take the 180 grit sandpaper and debur all the sharp edges off of the corners of the cam lobes too.
Want everything going together smooth.
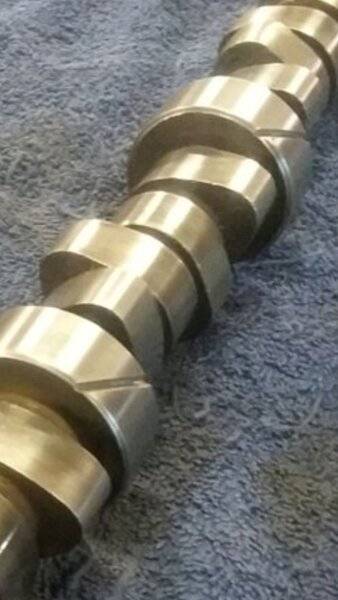