Neat video about bolts and nuts
Fascinating how much thought goes into some of this stuff.
Yep. The most accurate method is to measure the actual stretch of the fastener. Using a torque wrench replicates perfect lab conditions, meaning if you have too much resistance because threads are dirty, the torque wrench doesn't know that and you under stretch the bolt, if you lubricate a fastener but the specifications were intended for dry threads, you can cause it to go into yield. I always consult the manufacture or when I worked at the nuclear power plant, would go straight to engineering to clarify if the specification is for dry or lubricated and if lubricated, what lube?
There is a method used on cylinder heads and other applications called the torque-turn method. Where you torque to a value, (and torquing should always be done in 3 or 4 stages and in a cris-cross manner) and then turn so many degrees. A flat of a nut or bolt head is 30 degrees. That method originated in the railroad industry where when working on rails, a torque wrench is impractical. They would use a sledge hammer on a slugging wrench until the tone changed, indicating the joint was metal to metal, then slug it so many flats to get the stretch. In heavy industry like power plants, refineries, slugging wrenches are used daily.
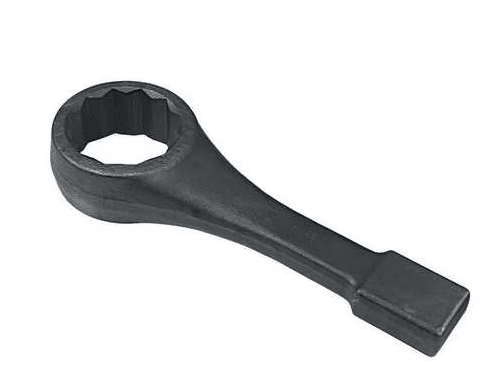
Another tool that is used is an hydraulic torque machine. Hytorc was the brand we used. There are several different styles of tool heads. Some use sockets, others have individual socket attachments. Again, torque in stages in a pattern till final torque, then "ring" the pattern at full torque psi. A pressure to torque conversion chart is used along with calibrated psi gauges. In the picture below, I'm not sure about the chaulk numbers as we would number the order so 2 would be across from 1 and so forth which I think makes it easier than looking at a drawing and interpreting that the 2nd to torque is #20 or whatever. Anyways, thought people might find this interesting.
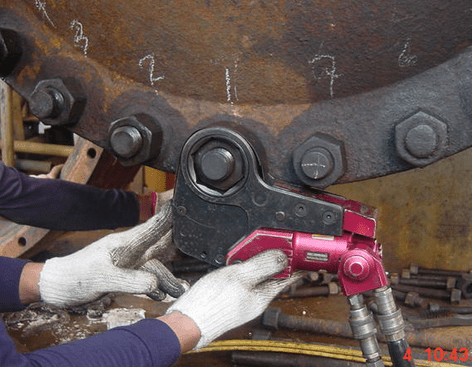