How to make torque boxes
I have been looking at threads about torque boxes for a while now, and the pre-made ones are gloriously expensive, so I decided to have a go at making my own. Not being too concerned with factory correctness, I drew up a sketch of what the front and rear would need to look like to accomplish the task of adding torsional stiffness to the body. Last week I stopped at Discount Steel and picked up a 2 X 4 piece of 14ga hot rolled steel for a little over $12.00. I was out in the shop Saturday morning and had nothing hot on the agenda, so I went ahead and fabricated up a set. Here is how it went;
Fortunately, the car is already on a rack that I made, so access was pretty easy.
Here is the front frame pocket that will get boxed in.
The rear frame pocket is more complex than the front, and an access hole needs to be created to get to the spring hanger fasteners.
I laid out the cut lines for the blanks and used my trusty Bosch jig saw to cut out pieces. Here is the front blank set in the frame to begin scribing to fit. Notice it needs to be bent a little as well.
All of the pieces needed to be bent to fit the frame, so I set up a jig in the bench vise with an angle iron. I clamped the blank in to the angle and then clamped a piece of ¼ plate to the sheet and used that to control the bend line. This is my version of a hillbilly sheet metal brake.
Here is the front drivers side test fit into place. The angle clears the fender fasteners and follows the front frame support. I still need to cut the drain hole in this piece.
Once the piece was scribed to fit, I tacked it in place, hammering around the welds where necessary to get the metal tight to the supports. That makes welding easier later.
The rear plate is more complex and has a sharp bend that needs to follow the frame rail. I used three bend lines to get it close, then I persuaded it into place. The weld in the lower section is where I needed to add metal due to the extra length of the bend angle.
Here I am cutting the spring fastener access hole. Note the air nozzle by the blade. I put that on the saw to keep the blade cool and blow the chips out of the cut. It works very well!
Here we go! Both front and rear boxes are fabbed and tacked in place and ready to weld up.
Same shot welded, cleaned up and primed.
Here is a rear detail showing the metal work around the access hole. I flared the metal out to add a little strength and to mimic the factory appearance.
Front detail showing the drain hole and bends. Pardon the weld along the body seam, I was having trouble getting the wire to feed smoothly. Always something to adjust!
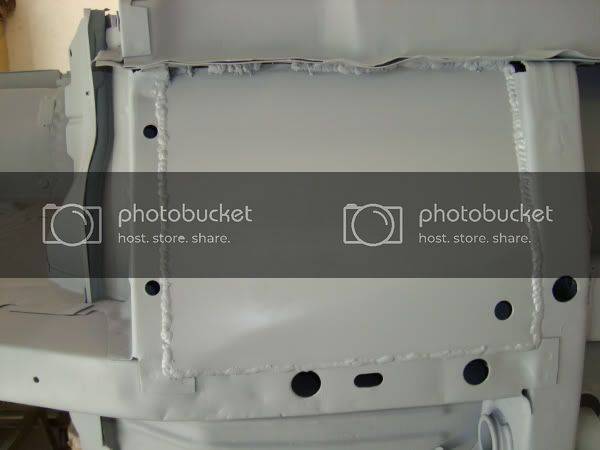