DaveBonds
Garage Trash
Decided to skip the adjustable link on the pedal. All that would do is adjust L arm to pedal distance, which I don't feel is necessary. The idea was to get the rack and cog adjusted to absolute ohm when the pedal is on its respective stop, but I went ahead and built the rack arm of the L linkage a little longer, so the linkage has 1/8" more throw than it needs, just to be sure.
I can just put a stop screw through a push spring on either end of the rack mount for stops and call it good. The pot has stops in it, but they are only designed to stop an index finger and thumb from cranking it further. I've got my foot on this thing, so I'd rather have the linkage rely on it's own stops, even with a set of pedal down & up stops. The pics don't show the linkage, but I moved the slotted hole down into the bottom hole of the vertical link. It has 3/16" of slide travel, which I think should be enough for the pedal travel to engage the pedal recognition and arc trigger switches, before moving the amps.
I'm still waiting on the CK line, transmitter/ receiver and a few odds and ends. I'm going to wait on the rest of the parts to arrive and test the transmitter/ receiver before I make the pedal casing. The sending unit/ key fob button may act as a spark gap transmitter (!!!) so I'm going to do some preliminary testing with me away from the torch and the transmitter on, in varying AC frequencies to see if it tries to jump to the transmitter or messes with the receiver relay output on my multimeter. Miller makes a wireless foot pedal, so I know this can be done, but I want to know that having a high frequency transmitter in my hand will be safe and work correctly.
It comes with two transmitters, so if I zap one, I guess I can use the other and receiver some other way. I thought about wiring the switch that is zip tied to the torch, down to the transmitter, a few feet below the trigger/ torch, still using the veclro for easy use. We'll see. Hopefully it just does what it's supposed to do.
If I'm using this pedal under low amp conditions and pulsing the pedal, I will be releasing it almost completely. There is a time delay on the gas, but I wonder if I should put a time delay off switch in the pedal recognition pins, or if it matters? I'll see what happens when I connect a micro switch and leads to the 6 and 7 pins to see how responsive it is. If its instant, I won't need a delay to keep it in foot pedal mode. If 6-7 activates a relay inside the welder, or if it's recognized digitally, may change my mind depending on how it processes to turn the pedal on. I'd rather not wear something out in the welder by having the 6-7 constantly switching, although it may not even be a valid concern and be like the trigger constantly switched or an arcade button and be able to take use all day long.
I think I'm going to put an adjustable light tension ball bearing index on the rack, at the very least, so I can hear and feel an audible click, aside from the micro switches, at min amps before the trigger is released, so I can dip down to min amps for pulsing without losing an arc. I'll just be sure to put a larger bearing in it than the dimple, so my foot has no problem running back out of the index with ease.
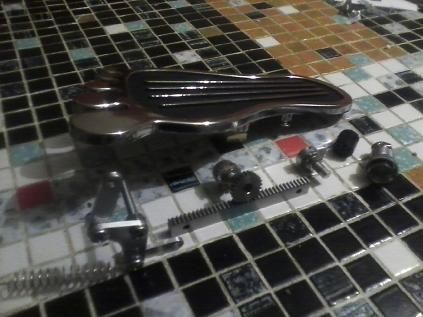
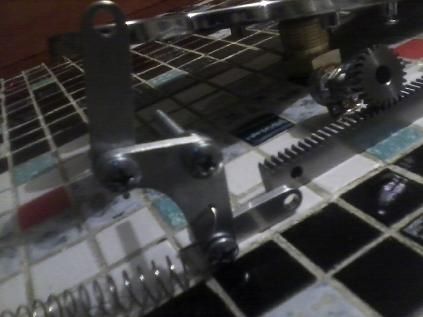
I can just put a stop screw through a push spring on either end of the rack mount for stops and call it good. The pot has stops in it, but they are only designed to stop an index finger and thumb from cranking it further. I've got my foot on this thing, so I'd rather have the linkage rely on it's own stops, even with a set of pedal down & up stops. The pics don't show the linkage, but I moved the slotted hole down into the bottom hole of the vertical link. It has 3/16" of slide travel, which I think should be enough for the pedal travel to engage the pedal recognition and arc trigger switches, before moving the amps.
I'm still waiting on the CK line, transmitter/ receiver and a few odds and ends. I'm going to wait on the rest of the parts to arrive and test the transmitter/ receiver before I make the pedal casing. The sending unit/ key fob button may act as a spark gap transmitter (!!!) so I'm going to do some preliminary testing with me away from the torch and the transmitter on, in varying AC frequencies to see if it tries to jump to the transmitter or messes with the receiver relay output on my multimeter. Miller makes a wireless foot pedal, so I know this can be done, but I want to know that having a high frequency transmitter in my hand will be safe and work correctly.
It comes with two transmitters, so if I zap one, I guess I can use the other and receiver some other way. I thought about wiring the switch that is zip tied to the torch, down to the transmitter, a few feet below the trigger/ torch, still using the veclro for easy use. We'll see. Hopefully it just does what it's supposed to do.
If I'm using this pedal under low amp conditions and pulsing the pedal, I will be releasing it almost completely. There is a time delay on the gas, but I wonder if I should put a time delay off switch in the pedal recognition pins, or if it matters? I'll see what happens when I connect a micro switch and leads to the 6 and 7 pins to see how responsive it is. If its instant, I won't need a delay to keep it in foot pedal mode. If 6-7 activates a relay inside the welder, or if it's recognized digitally, may change my mind depending on how it processes to turn the pedal on. I'd rather not wear something out in the welder by having the 6-7 constantly switching, although it may not even be a valid concern and be like the trigger constantly switched or an arcade button and be able to take use all day long.
I think I'm going to put an adjustable light tension ball bearing index on the rack, at the very least, so I can hear and feel an audible click, aside from the micro switches, at min amps before the trigger is released, so I can dip down to min amps for pulsing without losing an arc. I'll just be sure to put a larger bearing in it than the dimple, so my foot has no problem running back out of the index with ease.