Dusterdude72
IN MOPAR MUSCLE MAGAZINE
Well, got a late start today so I didnt get much done really. BUT, I do have some picture updates.
I played hell with getting the old tail panel off......first of all, the easy part was melting the led out of the seems.
finding all the spot welds was a little bit tricky but nothing major.
the worst part was .....the previous owner removed the trunk pan and replaced it with a flat sheet of steel.....and when he welded it in, he welded it to the back side of the tail panel.
which made it extra work for me to remove it.
he also used spray foam everywhere ( I hate that stuff ) it holds moisture and is a B!t#h to get out of the nooks and crannies.
now I need to get some steel so I can rebuild the little end caps that go in the lower corners of the tail panel that connect the tail panel to the quarter panels ( slipping my mind on what the exact name for the little panels are at the moment ).
I also need to get some steel and make a channel out of angle iron to connect the floor to the backside of the tail panel because when the previous owner replaced the trunk pan he left the steel that connects the pan to the tail panel and its pretty weak and rusty so I am going to get rid of it and make my own.
then I am going to use rust converter on everything .
then I will install the new tail panel and move on to installing the new lower quarter panel patches.
it doesnt look the prettiest at the moment but in time ill have her looking good.
here is a picture of the old panel (don't let it fool you, 50% of what you see has bondo under it...plus the rust.....was definitely time for a new panel!)
and another picture of right after I pulled the panel (don't mind all the crap in the trunk ....thats the "duster parts/overflow storage compartment" lol).
and another picture where I placed the new panel in the opening just to get an idea of what it would look like!.
I played hell with getting the old tail panel off......first of all, the easy part was melting the led out of the seems.
finding all the spot welds was a little bit tricky but nothing major.
the worst part was .....the previous owner removed the trunk pan and replaced it with a flat sheet of steel.....and when he welded it in, he welded it to the back side of the tail panel.
which made it extra work for me to remove it.
he also used spray foam everywhere ( I hate that stuff ) it holds moisture and is a B!t#h to get out of the nooks and crannies.
now I need to get some steel so I can rebuild the little end caps that go in the lower corners of the tail panel that connect the tail panel to the quarter panels ( slipping my mind on what the exact name for the little panels are at the moment ).
I also need to get some steel and make a channel out of angle iron to connect the floor to the backside of the tail panel because when the previous owner replaced the trunk pan he left the steel that connects the pan to the tail panel and its pretty weak and rusty so I am going to get rid of it and make my own.
then I am going to use rust converter on everything .
then I will install the new tail panel and move on to installing the new lower quarter panel patches.
it doesnt look the prettiest at the moment but in time ill have her looking good.
here is a picture of the old panel (don't let it fool you, 50% of what you see has bondo under it...plus the rust.....was definitely time for a new panel!)
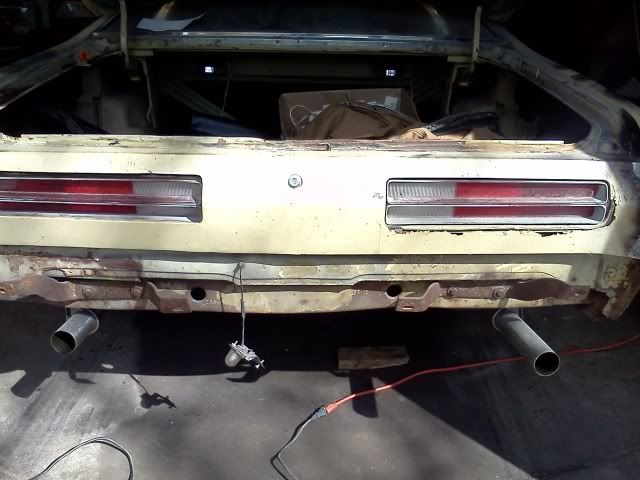
and another picture of right after I pulled the panel (don't mind all the crap in the trunk ....thats the "duster parts/overflow storage compartment" lol).
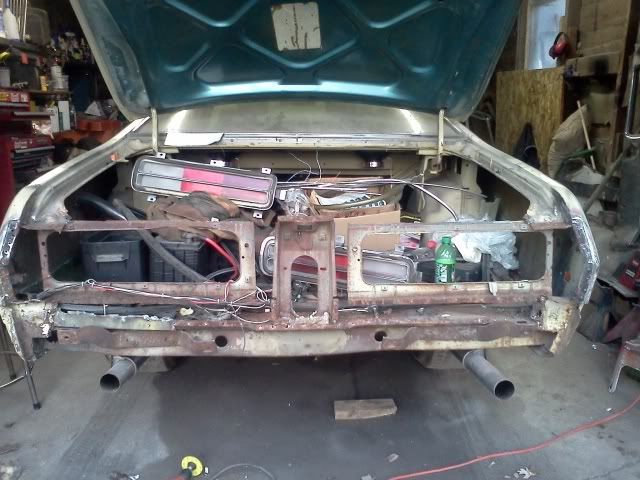
and another picture where I placed the new panel in the opening just to get an idea of what it would look like!.
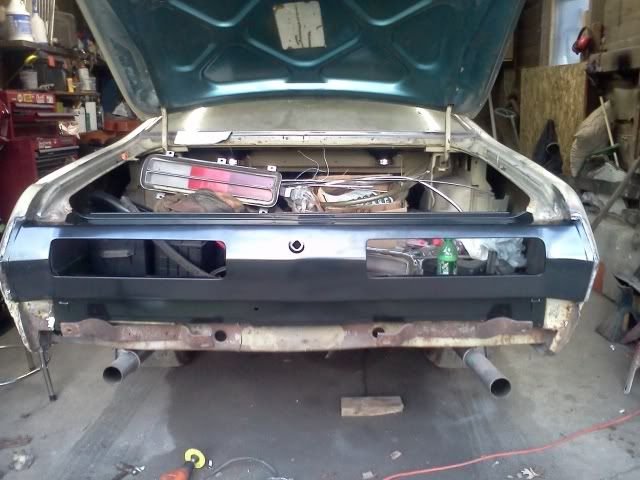