A tale of woe and sorrow....
My wife, Dena, and I were all set to spend some bonding time together by doing one of the rear seat cushions in the living room. Thought it might be nice. After I was done fussing with the aforementioned details, I set the frames on the living room rug and retrieved the first of the soft goods to be installed; the burlap. I unroll the material on the floor and immediately my nose curled to what smelled like kerosene. I say to Dena, "hey, this smells like it's been treated with something." No sooner had the words left my mouth, the missus is telling me, "get that **** out of here!!" The whole room filled up with the foul smell of lamp oil, diesel, hell I don't even know what all.
I tossed it all out the front door and after Dena opened all the windows and turned up the ceiling fans, she sat out back to google
what do they treat burlap with? Turns out, it's lots of things. Fungicides, pesticides, anti-rot. Who knew?
Now the fun begins. Can we launder this out?
Before tossing the fabric in our machine, I thought it would be a good idea to try and hand wash the heaviest contamination in the utility sink. Hot water, baking soda, and some dish soap produced this:
After a rinse and second wash, we got this:
Having murdered all of the flora in my septic tank, I wrung out the cloth and draped it over a step ladder outside to air dry. The next day, it still stank like it had been marinated in gasoline. I give up.
Off we go to the fabric store in search of some untreated burlap. $12 later, I come home with a far lighter smelling roll of yardage and begin the same laundering process.
Difference in burlaps:
But after a good hand washing and two trips through the wash machine, the burlap still smelled of lamp oil and the shedding was
off the chain. I hung it on said stepladder to dry and, just doing that, it dropped a ton of loose fiber.
No, that's not his fuzz. Even he doesn't shed this bad!
More reading on the Internet and I conclude that burlap is **** if you have to treat it with so much toxic waste in order for it to not rot, be consumed by mice, harbor mold, etc. Screw all that. Another fabric will be substituted here.
Feeling right at home amongst the mass quantities of lint.
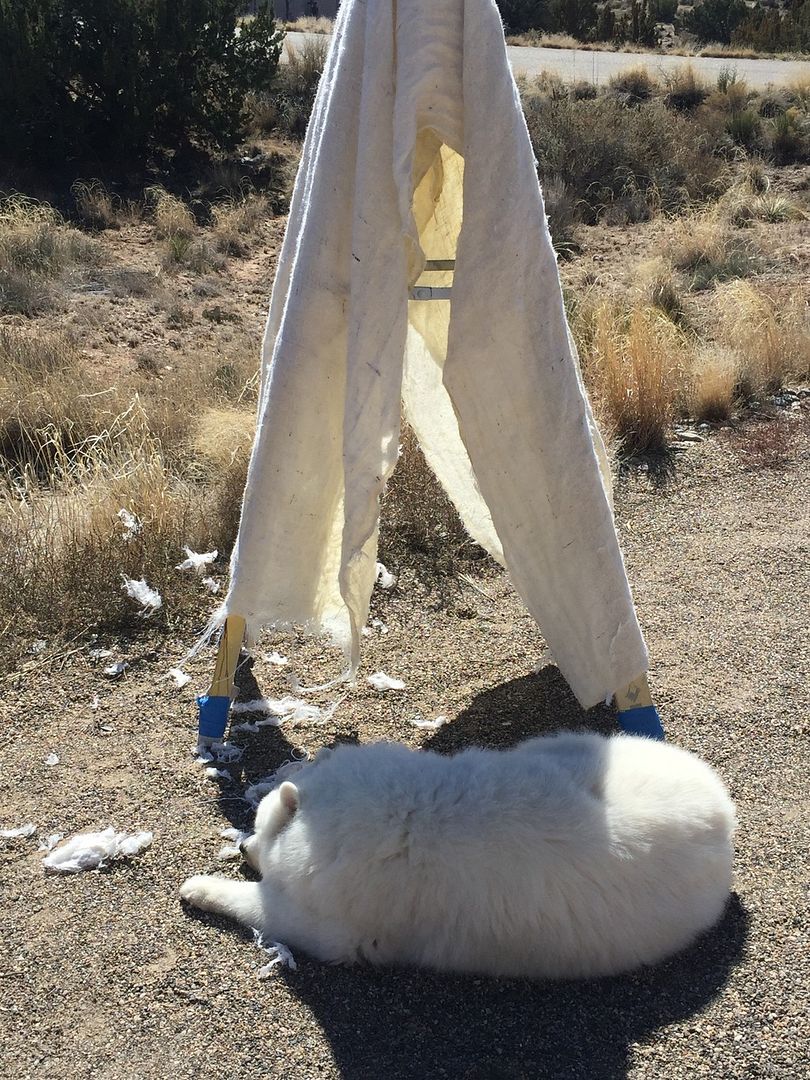