I recently rebuilt a 69 Barracuda Wiper Motor. I took a bunch of pictures to help me get it back together, but I only thought to write a How-To article about halfway through. So I will be missing a few pictures showing disassembly, but I will use some ‘after’ pictures when needed. I included instructions on how to properly test the finished product in step 17 below. Refer to that if you want to test it first, which I think you should. Even though I have provided pictures below, I would still recommend taking lots of your own. Plus, bag and tag all clips, washers, etc. and carefully note where they came from. You can probably tell where they go by the attached pictures, but it is a good habit to get into.
1. Thoroughly clean it before disassembly. It makes the job much more pleasant. I hope yours is not as dirty as this one.
Picture 1.
2. Remove the resistor. It gives you low speed.
3. Remove the rotating arm (“A” in picture 2) and the rubber cap (“B”).
Picture 2
4. Remove the spring clip under the rubber cap as seen in picture 3.
Picture 3
5. Remove the three grommets. It may be easier to cut them out. They are easily available.
6. Remove the cylindrical housing by removing the two long screws circled in blue in picture 4. The rotor (or armature) is inside. When you pull off the housing, the powerful magnets inside it will likely pull out the rotor. If not, it should come out easily. When you pull out the rotor, the three brushes will pop out of their slots. No problem. They are easy to put back later. Plus, how they are situated makes it pretty much impossible to put them in wrong. Picture 5 shows the rotor’s position inside the cylindrical housing. Picture 8 shows the brushes after the rotor has been pulled out.
Picture 4
Picture 5
7. Drill out all the rivets holding the two remaining halves of the wiper assembly together. There should be six of them. I think I used a 5/32 bit. When you pull the two halves apart, make sure you do it carefully. You don’t want any small parts to pop out and disappear (although they will probably be stuck in with hardened, 50 year old grease). Picture 6 is an after picture, but it is what you should see now. The worm gear on the left (A) will not be present since you already pulled out the rotor. Notice that there are 3 washers (B) on the shaft above the large gear on the right. There is a spring washer in between two flat washers. They may be buried in dirty grease. Make sure you get them. Then pull that large gear out. There will be a washer on the bottom of the shaft also. Then pull the smaller gear on the left (C) up off the shaft. There is a tiny spring washer below it. It may be stuck to the gear or the bottom of the housing. You can see that spring washer circled in blue in picture 7 below. It is also circled with a #1 in picture 10.
Picture 6
Picture 7
8. Take off the hard plastic piece that contains the four electric terminals and the brushes. It is held in with two rivets, and it is circled in blue in picture 8.
Picture 8.
9. Take a look at the ‘Park’ assembly. It is labeled as “D” in picture 6. Note that it is under the large gear. Picture 9 is the back side of the plastic part circled in blue in picture 8. Picture 9 shows a better view of what you see as “D” in Picture 6. The shorter brass part and the taller copper part are attached to the two terminals labeled P1 and P2 in picture 20. The brass piece is fixed, and the longer copper piece moves as it hits a bump on the back side of the large gear on the right in picture 6. It is important to get the copper and brass parts CLEAN so they can make a good circuit when they touch when the bump on the gear moves the copper piece.
Picture 9
10. CLEAN everything thoroughly. Sandblast most parts to be painted if you can. If you don’t have access to a blasting cabinet, you can scuff with sandpaper. I would scuff everything while it is apart and once more after assembly. By scuffing parts now, it will be easier to hit the places that will be hard to get when assembled. During assembly, try to keep from getting grease on anything that will be painted. I am sure there are multiple ways to assemble this. I am just going to give you one possible way. Picture 10 shows all the loose pieces (short of the three large metal housing parts) you should have at this time.
Picture 10
11. Attach the hard plastic piece that contains the four electric terminals and the brushes (from step 8 above) to the shell half it came from. I used 8x32 machine bolts. My parts have black on them now, because I powder coated. I assume 99.9% of you will be painting after final assembly, so your parts will all be bare now. There is a spring that retains each brush. Place the brushes back into their slots (as seen in picture 8). Then gently push them all the way back into the slot. The spring will ‘click’ and hold the brushes into place. Put a little grease on the three washers that go on the rotor shaft (circled with a #2 in picture 10), and then place them on the shaft of the rotor, as seen in picture 11 below (spring washer in the middle). Then apply some grease on the shaft where it will ride in the bushing in the metal shell below the brushes (pretty much where the three washers are in picture 11) and slide the rotor into position as seen in picture 12 below. Then with a small, thin, flat bladed screwdriver, gently push each brush towards the center. They should ‘pop’ into place.
Picture 11
Picture 12
12. Using the two long screws circled in blue in picture 4, attach the cylindrical rotor housing from step 6 above onto the rotor/shell assembly from step 11.
13. Place some grease on small spring washer (circled with a #1 in picture 10) and place it on the shaft sticking up from the housing as seen in picture 13 below. Then slide the washer to the bottom, grease the shaft and slide the gear (C in picture 6) onto the shaft. Grease the gear up a little before installation.
Picture 13
14. First, place the last washer from picture 14 (circled in blue with a “C”) over the shaft circled in blue with an “A” in picture 14. Then place some grease on the bottom 1/2 " of the shaft circled in blue with an “A” in Picture 14. Don’t get too much grease on the very bottom tip or the shaft will not fit to the proper depth in the hole containing the bushing. Then place the gear into the housing as seen circled in blue in picture 15 below. When installing this gear, BE CAREFUL NOT to bend the long copper piece that is part of the "Park" assembly (also seen in picture 9 above). Grease the gear up a little before installation. Don’t be concerned if this gear rubs against the one from step 13 now. It won’t when you tighten the nut in step 19, as that will draw the shaft up a bit.
Picture 14
Picture 15
15. Place the three washers over the threaded end of the shaft as seen in picture 16 below. This picture was taken before it was cleaned. The spring clip goes on after the shaft goes through the housing. I just have the spring clip temporarily installed to show the order of all four pieces. All you are doing in this step is putting on the three washers with the spring washer in the middle. Place a dab of grease on the washers. Note that the three washers will be below the housing (and unseen) and the spring clip will be above the housing. Then grease the shaft where it will contact the bushing in the housing place the housing over the threaded shaft. You probably will not be able to attach the clip at this time.
Picture 16
16. Fasten the two sides of the motor together. I used 8x32x3/8” machine bolts and nuts as seen in picture 17. You may have to drill the holes out a teeny bit for this, or you could use 6x32 bolts, which I think are too small. Decision time. You can leave the machine bolts in, or you can rivet it together by pulling the bolts out one at a time and inserting rivets. Even if you plan to rivet it together, I think it is important to do it with the machine bolts first. That way you can test it now, and if (HOPEFULLY NOT) it didn’t work, you are not drilling out rivets. The motor in picture 17 below is black because I powder coated the metal parts before assembly. I would not have been able to put the assembled unit in a 400 degree powder coating oven with grease and nylon gears inside. 99.9% of you will be painting yours, so yours will be bare metal now.
Picture 17
17. Test it! I have included shots of assembly manual pages for testing the motor. Since the picture depicting the terminal names is not very good, I included a better one.
Picture 18
Picture 19
Picture 20
18. Assuming it tested OK, either leave the bolts and nuts in, or take them out one at a time and use short 5/32” pop rivets. Don’t forget to put on the grounding strap as seen in the blue square in the ‘before’ picture 8 above. If desired, you can fill in the small holes in the rivets with a bit of epoxy to hide them before painting.
19. Install the clip as seen in picture 21 below. Then install the rubber cap (picture 22). Then install the rotating arm as seen in picture 2 above (it will only go on one way) and tighten the nut. I don’t know the torque, just make it snug.
Picture 21
Picture 22
20. Paint it with your choice of Semi-Gloss Black paint. Make sure you mask the four electric terminals. Then CAREFULLY install new grommets. Dorman part# 49450 for $5 work and look fine.
1. Thoroughly clean it before disassembly. It makes the job much more pleasant. I hope yours is not as dirty as this one.
Picture 1.
2. Remove the resistor. It gives you low speed.
3. Remove the rotating arm (“A” in picture 2) and the rubber cap (“B”).
Picture 2
4. Remove the spring clip under the rubber cap as seen in picture 3.
Picture 3
5. Remove the three grommets. It may be easier to cut them out. They are easily available.
6. Remove the cylindrical housing by removing the two long screws circled in blue in picture 4. The rotor (or armature) is inside. When you pull off the housing, the powerful magnets inside it will likely pull out the rotor. If not, it should come out easily. When you pull out the rotor, the three brushes will pop out of their slots. No problem. They are easy to put back later. Plus, how they are situated makes it pretty much impossible to put them in wrong. Picture 5 shows the rotor’s position inside the cylindrical housing. Picture 8 shows the brushes after the rotor has been pulled out.
Picture 4
Picture 5
7. Drill out all the rivets holding the two remaining halves of the wiper assembly together. There should be six of them. I think I used a 5/32 bit. When you pull the two halves apart, make sure you do it carefully. You don’t want any small parts to pop out and disappear (although they will probably be stuck in with hardened, 50 year old grease). Picture 6 is an after picture, but it is what you should see now. The worm gear on the left (A) will not be present since you already pulled out the rotor. Notice that there are 3 washers (B) on the shaft above the large gear on the right. There is a spring washer in between two flat washers. They may be buried in dirty grease. Make sure you get them. Then pull that large gear out. There will be a washer on the bottom of the shaft also. Then pull the smaller gear on the left (C) up off the shaft. There is a tiny spring washer below it. It may be stuck to the gear or the bottom of the housing. You can see that spring washer circled in blue in picture 7 below. It is also circled with a #1 in picture 10.
Picture 6
Picture 7
8. Take off the hard plastic piece that contains the four electric terminals and the brushes. It is held in with two rivets, and it is circled in blue in picture 8.
Picture 8.
9. Take a look at the ‘Park’ assembly. It is labeled as “D” in picture 6. Note that it is under the large gear. Picture 9 is the back side of the plastic part circled in blue in picture 8. Picture 9 shows a better view of what you see as “D” in Picture 6. The shorter brass part and the taller copper part are attached to the two terminals labeled P1 and P2 in picture 20. The brass piece is fixed, and the longer copper piece moves as it hits a bump on the back side of the large gear on the right in picture 6. It is important to get the copper and brass parts CLEAN so they can make a good circuit when they touch when the bump on the gear moves the copper piece.
Picture 9
10. CLEAN everything thoroughly. Sandblast most parts to be painted if you can. If you don’t have access to a blasting cabinet, you can scuff with sandpaper. I would scuff everything while it is apart and once more after assembly. By scuffing parts now, it will be easier to hit the places that will be hard to get when assembled. During assembly, try to keep from getting grease on anything that will be painted. I am sure there are multiple ways to assemble this. I am just going to give you one possible way. Picture 10 shows all the loose pieces (short of the three large metal housing parts) you should have at this time.
Picture 10
11. Attach the hard plastic piece that contains the four electric terminals and the brushes (from step 8 above) to the shell half it came from. I used 8x32 machine bolts. My parts have black on them now, because I powder coated. I assume 99.9% of you will be painting after final assembly, so your parts will all be bare now. There is a spring that retains each brush. Place the brushes back into their slots (as seen in picture 8). Then gently push them all the way back into the slot. The spring will ‘click’ and hold the brushes into place. Put a little grease on the three washers that go on the rotor shaft (circled with a #2 in picture 10), and then place them on the shaft of the rotor, as seen in picture 11 below (spring washer in the middle). Then apply some grease on the shaft where it will ride in the bushing in the metal shell below the brushes (pretty much where the three washers are in picture 11) and slide the rotor into position as seen in picture 12 below. Then with a small, thin, flat bladed screwdriver, gently push each brush towards the center. They should ‘pop’ into place.
Picture 11
Picture 12
12. Using the two long screws circled in blue in picture 4, attach the cylindrical rotor housing from step 6 above onto the rotor/shell assembly from step 11.
13. Place some grease on small spring washer (circled with a #1 in picture 10) and place it on the shaft sticking up from the housing as seen in picture 13 below. Then slide the washer to the bottom, grease the shaft and slide the gear (C in picture 6) onto the shaft. Grease the gear up a little before installation.
Picture 13
14. First, place the last washer from picture 14 (circled in blue with a “C”) over the shaft circled in blue with an “A” in picture 14. Then place some grease on the bottom 1/2 " of the shaft circled in blue with an “A” in Picture 14. Don’t get too much grease on the very bottom tip or the shaft will not fit to the proper depth in the hole containing the bushing. Then place the gear into the housing as seen circled in blue in picture 15 below. When installing this gear, BE CAREFUL NOT to bend the long copper piece that is part of the "Park" assembly (also seen in picture 9 above). Grease the gear up a little before installation. Don’t be concerned if this gear rubs against the one from step 13 now. It won’t when you tighten the nut in step 19, as that will draw the shaft up a bit.
Picture 14
Picture 15
15. Place the three washers over the threaded end of the shaft as seen in picture 16 below. This picture was taken before it was cleaned. The spring clip goes on after the shaft goes through the housing. I just have the spring clip temporarily installed to show the order of all four pieces. All you are doing in this step is putting on the three washers with the spring washer in the middle. Place a dab of grease on the washers. Note that the three washers will be below the housing (and unseen) and the spring clip will be above the housing. Then grease the shaft where it will contact the bushing in the housing place the housing over the threaded shaft. You probably will not be able to attach the clip at this time.
Picture 16
16. Fasten the two sides of the motor together. I used 8x32x3/8” machine bolts and nuts as seen in picture 17. You may have to drill the holes out a teeny bit for this, or you could use 6x32 bolts, which I think are too small. Decision time. You can leave the machine bolts in, or you can rivet it together by pulling the bolts out one at a time and inserting rivets. Even if you plan to rivet it together, I think it is important to do it with the machine bolts first. That way you can test it now, and if (HOPEFULLY NOT) it didn’t work, you are not drilling out rivets. The motor in picture 17 below is black because I powder coated the metal parts before assembly. I would not have been able to put the assembled unit in a 400 degree powder coating oven with grease and nylon gears inside. 99.9% of you will be painting yours, so yours will be bare metal now.
Picture 17
17. Test it! I have included shots of assembly manual pages for testing the motor. Since the picture depicting the terminal names is not very good, I included a better one.
Picture 18
Picture 19
Picture 20
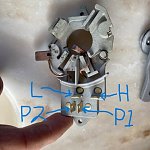
18. Assuming it tested OK, either leave the bolts and nuts in, or take them out one at a time and use short 5/32” pop rivets. Don’t forget to put on the grounding strap as seen in the blue square in the ‘before’ picture 8 above. If desired, you can fill in the small holes in the rivets with a bit of epoxy to hide them before painting.
19. Install the clip as seen in picture 21 below. Then install the rubber cap (picture 22). Then install the rotating arm as seen in picture 2 above (it will only go on one way) and tighten the nut. I don’t know the torque, just make it snug.
Picture 21
Picture 22
20. Paint it with your choice of Semi-Gloss Black paint. Make sure you mask the four electric terminals. Then CAREFULLY install new grommets. Dorman part# 49450 for $5 work and look fine.