FomocoReformed
Well-Known Member
Ok so I finally managed to get all the brackets and junk off my axle tubes. Cut the drivers side today with my chop saw and even though I measured it a gazillion times I still cut it a little short. Not by much, but shorter than I wanted to.
It came out to around 3/16 too short, I'm guessing the width of the saw wheel took off more than I anticipated it would. Regardless, I have a few options I've come up but I'm not sure what the best idea would be, make your choices.
Option 1, I measured the bearing surface on the axle shaft itself and it looks like I've got about 4/16 of space from where the bearing originally would have sat before the bearing surface tapers down. I could probably weld my tube back together and get away with it having 1/16 to spare.
Option 2, leave a small 1/16 or 2/16 gap between the two pieces of tube, fill it in with weld. Would get me more comfortably close.
Option 3, try to shave a 3/16 spacer out of the chunk of tube I cut out already, weld that between the two halves. Probably going to be a PITA to actually cut. I'm expecting this to be very difficult to get straight and the welds on either side will probably just run into each other and eat up the spacer.
This is about what I'm working with here,
It came out to around 3/16 too short, I'm guessing the width of the saw wheel took off more than I anticipated it would. Regardless, I have a few options I've come up but I'm not sure what the best idea would be, make your choices.
Option 1, I measured the bearing surface on the axle shaft itself and it looks like I've got about 4/16 of space from where the bearing originally would have sat before the bearing surface tapers down. I could probably weld my tube back together and get away with it having 1/16 to spare.
Option 2, leave a small 1/16 or 2/16 gap between the two pieces of tube, fill it in with weld. Would get me more comfortably close.
Option 3, try to shave a 3/16 spacer out of the chunk of tube I cut out already, weld that between the two halves. Probably going to be a PITA to actually cut. I'm expecting this to be very difficult to get straight and the welds on either side will probably just run into each other and eat up the spacer.
This is about what I'm working with here,
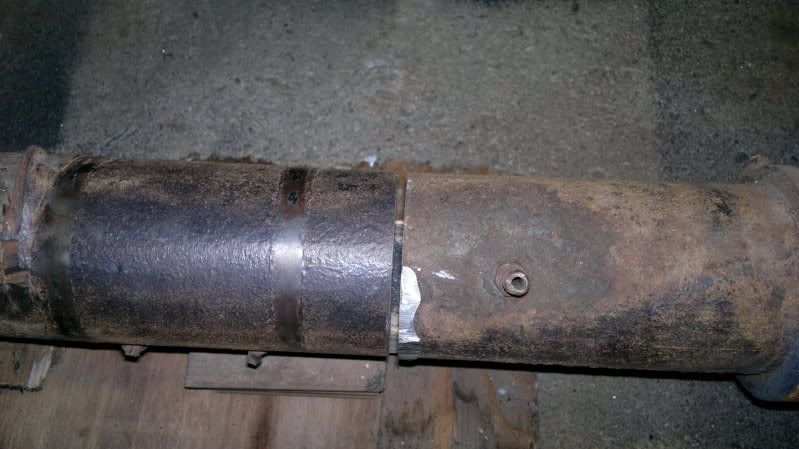