/6 Matt
30 Degrees Crooked
Well, I finally have a job now and I'm going to start sometime next week after a year an a half job search with no calls or interviews, thank goodness.
Today was the first day of my senior year in high school and because I'm going to school in Burke County, the only county in NC that I'm aware has this graduation requirement, I have to do a senior project. You write a paper, do a project and make a speech. I have to pick a mentor for the project portion and yada yada. But I have a two barrel and an intake to put on the car someday and I'd like some headers. I don't know how to weld but I'm confident I peice together a set of two piece headers as I was in drafting last year and I acceled so fast in there I actually took measurements off my two barrel intake during my freetime in class to make a three barrel intake. I've pieced together quite alot of things in my time working at my best friend's dad's body shop so I'm good at the assembly. Well I figure why not have my friend's dad teach me to weld and set me free on it.
I know I need a header flange if there is a good one out there or I can make one myself with a metal plate. I need to know what kind of metal plate, I do believe I'd need carbon steel right? That's what the make exhaust pipes out of if I'm not mistaken. How thick should the plate be? On the actual exaust tubes for the headers. how big should the primary tubes be? I wanna use two inch collectors and run them open because my car is so old, I don't have to get it inspected. No noise ordinances either. Is there anything I'm forgetting to ask? Am I making this project sound easier in my head than it actually will be?
I'll probably have more questions shortly after I post this. And by the way, here's that manifold.
On a side note, some of looks you get when you carry around a cast Iron two barrel intake in school, you get some funny looks and questions.
Today was the first day of my senior year in high school and because I'm going to school in Burke County, the only county in NC that I'm aware has this graduation requirement, I have to do a senior project. You write a paper, do a project and make a speech. I have to pick a mentor for the project portion and yada yada. But I have a two barrel and an intake to put on the car someday and I'd like some headers. I don't know how to weld but I'm confident I peice together a set of two piece headers as I was in drafting last year and I acceled so fast in there I actually took measurements off my two barrel intake during my freetime in class to make a three barrel intake. I've pieced together quite alot of things in my time working at my best friend's dad's body shop so I'm good at the assembly. Well I figure why not have my friend's dad teach me to weld and set me free on it.
I know I need a header flange if there is a good one out there or I can make one myself with a metal plate. I need to know what kind of metal plate, I do believe I'd need carbon steel right? That's what the make exhaust pipes out of if I'm not mistaken. How thick should the plate be? On the actual exaust tubes for the headers. how big should the primary tubes be? I wanna use two inch collectors and run them open because my car is so old, I don't have to get it inspected. No noise ordinances either. Is there anything I'm forgetting to ask? Am I making this project sound easier in my head than it actually will be?
I'll probably have more questions shortly after I post this. And by the way, here's that manifold.
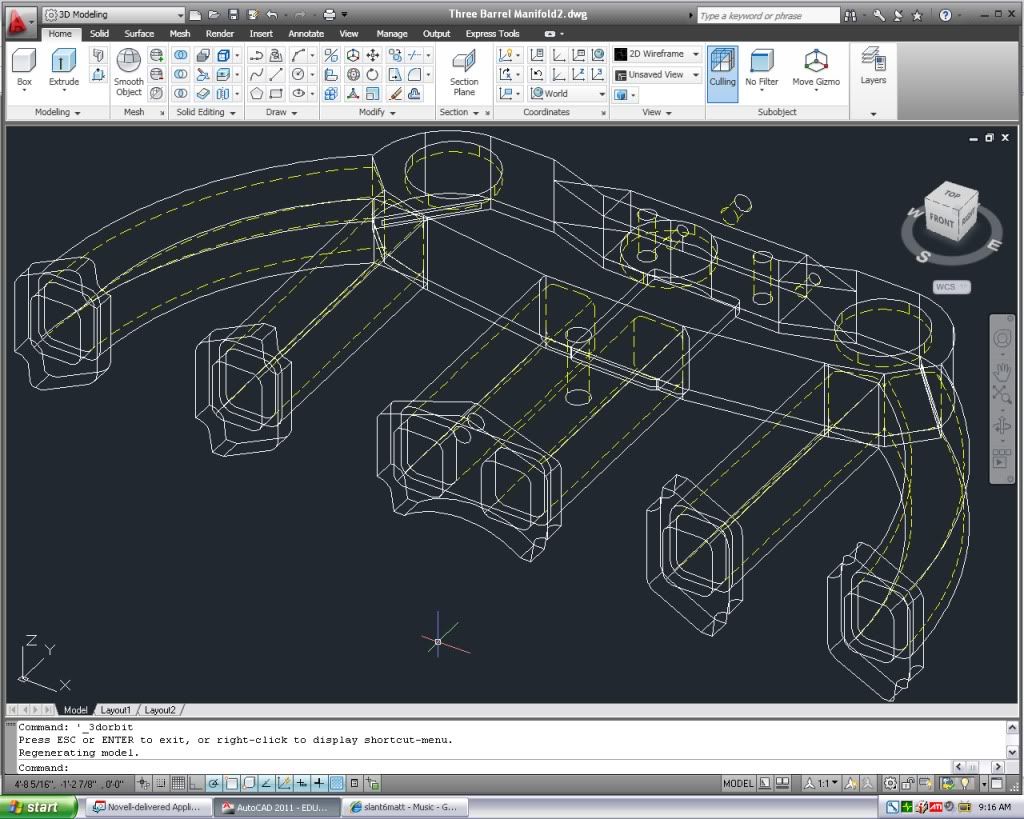
On a side note, some of looks you get when you carry around a cast Iron two barrel intake in school, you get some funny looks and questions.