flyboy01
Its almost done!
I have a few questions, it has been about 15 years since I last used to weld, it seems that I forgot everything I knew about welding.
I recently bought a small Lincoln 110v welder, I am usung pure C02 with it. The issue I am having seems to be dirty Welds when I was welding up some 1/4 holes, the smaller holes looked fine, but the beads are sticking up to far, I have to do a lot of grinding to get them flat. I have the regultaor set on 30psi for the C02, which was recommender my Lincoln tech support.
What is a good pressure?
Why are my welds so tall?
Why all the soot?
I recently bought a small Lincoln 110v welder, I am usung pure C02 with it. The issue I am having seems to be dirty Welds when I was welding up some 1/4 holes, the smaller holes looked fine, but the beads are sticking up to far, I have to do a lot of grinding to get them flat. I have the regultaor set on 30psi for the C02, which was recommender my Lincoln tech support.
What is a good pressure?
Why are my welds so tall?
Why all the soot?
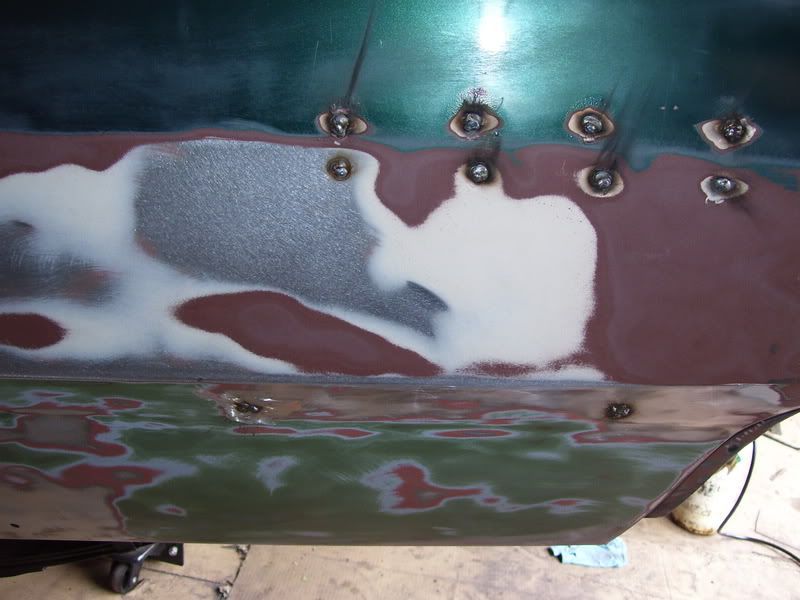
