mopowers
Well-Known Member
I need to drill and tap the 1/4" NPT hole just left of the water neck in my Air-gap manifold to accept a 3/8" NPT fitting. Since I've never tapped a NPT hole before, I've got a quick question...
Seeing how the threads are tapered, how deep do I need to run the tap??? I've heard 12 threads deep is the go-to number. Or should I tap it and keep test fitting the fitting until I'm happy with the depth?
Seeing how the threads are tapered, how deep do I need to run the tap??? I've heard 12 threads deep is the go-to number. Or should I tap it and keep test fitting the fitting until I'm happy with the depth?
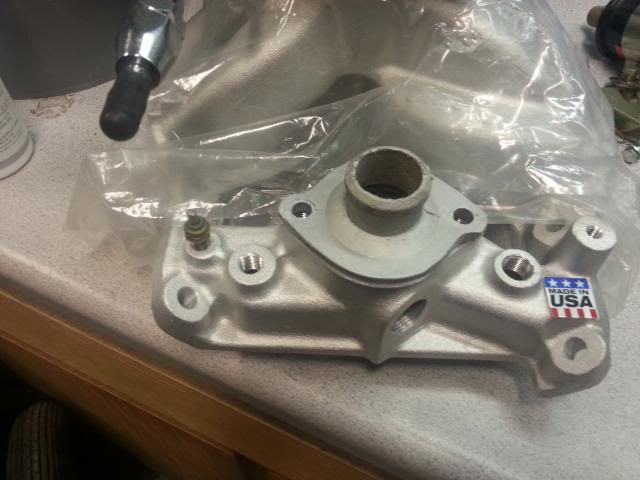