Ok guys, so this is what I'm dealing with. The previous owner made swiss cheese out of my firewall trying to install power brakes. I decided to fix the problem by cutting the firewall out and welding in a new replacement panel in its place. I just bought an automatic brake pedal w/ mount out of a 75 Valiant and I need to mock up the holes for the studs that mount the MC to go though.
Just to let you know, I plan on installing a NAPA Master Cylinder for a 1980 Diplomat converting it over to manual brakes. It has a 1 1/32 bore and is of the 2 hole mount. I was also planning on buying the 4 to 2 master cylinder adapter plate from someone.
Unfortunately, I'm not really sure how I'd go about doing this. One member mentioned pressing out the studs from the brake mount and installing the brake pedal marking where to cut the holes on the firewall. Thanks for your help in advance.
Also, what would be a good way to clean the welds more. My main problem is that I've got wire awfully close to the firewall and I don't want to cut those as electrical circuits is complete black magic to me. :banghead:
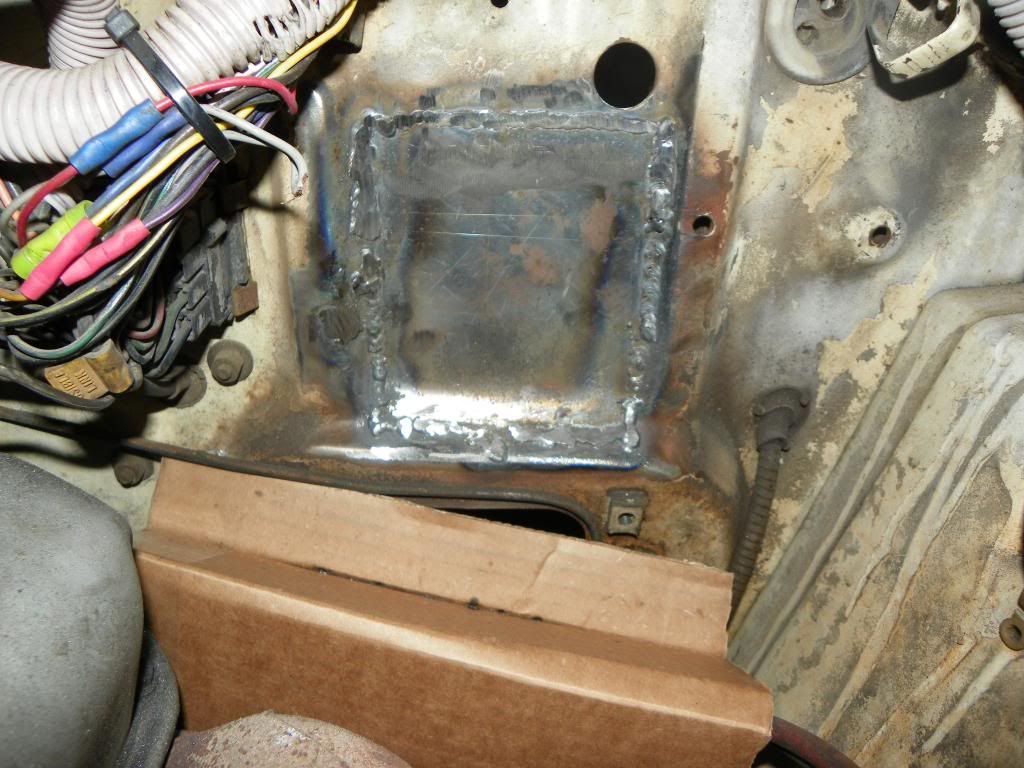
Just to let you know, I plan on installing a NAPA Master Cylinder for a 1980 Diplomat converting it over to manual brakes. It has a 1 1/32 bore and is of the 2 hole mount. I was also planning on buying the 4 to 2 master cylinder adapter plate from someone.
Unfortunately, I'm not really sure how I'd go about doing this. One member mentioned pressing out the studs from the brake mount and installing the brake pedal marking where to cut the holes on the firewall. Thanks for your help in advance.
Also, what would be a good way to clean the welds more. My main problem is that I've got wire awfully close to the firewall and I don't want to cut those as electrical circuits is complete black magic to me. :banghead:
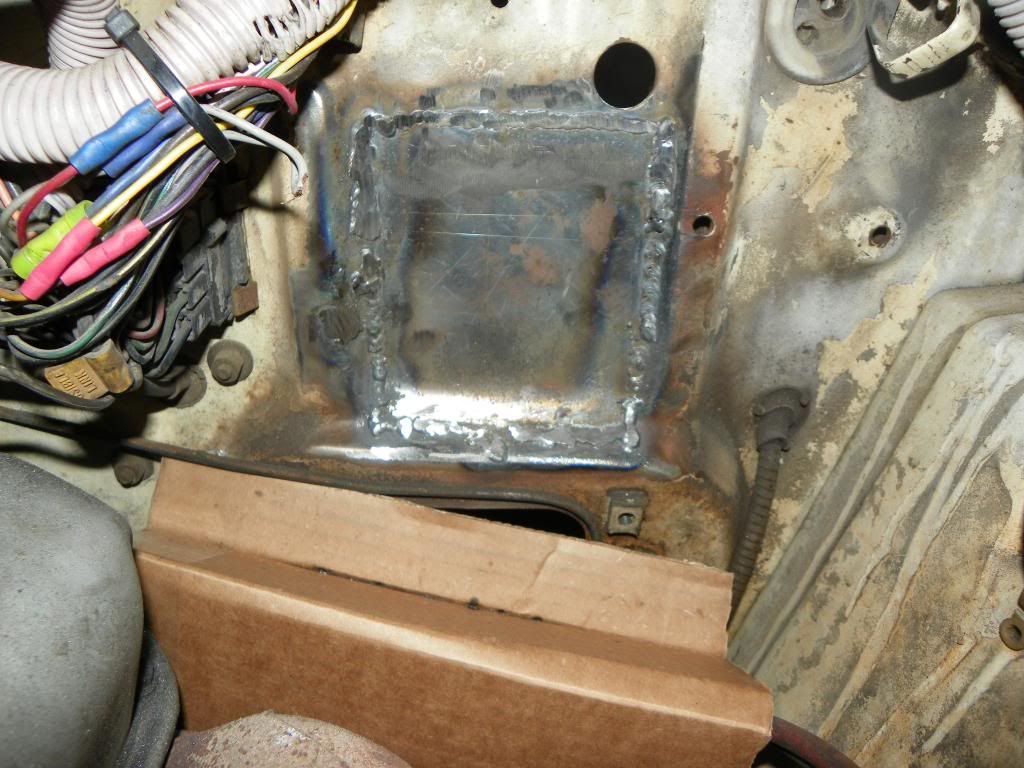