Cope
Fusing with fire
My motor builder buddy showed up at the shop today and comments that my intake valves are to big.
He is saying I need to cut way more out of the combustion chamber, turn the valve heads down or stroke the motor. (440)
Now before you go and say this guy dont know jack, He builds very high end (30-50K) race motors that win races and He build them every day for a living.
What are your folks thoughts on this?
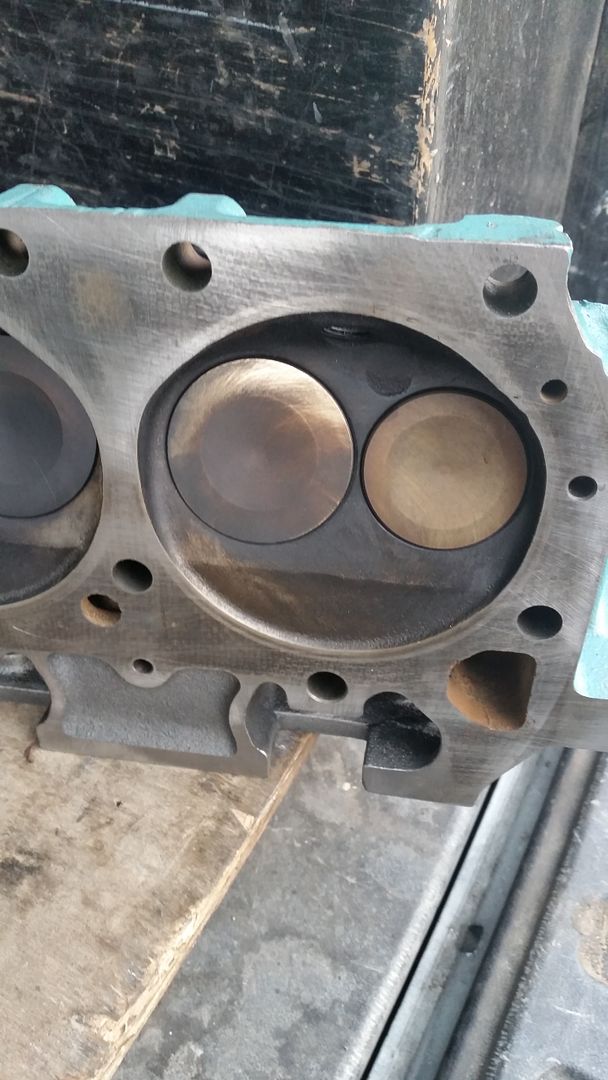
906 heads, 2.118 intake. I think thats what they mic out to. I will double check the size tomarrow.
He did say the exhaust valve size is fine.
Thanls again for the time and advice.
He is saying I need to cut way more out of the combustion chamber, turn the valve heads down or stroke the motor. (440)
Now before you go and say this guy dont know jack, He builds very high end (30-50K) race motors that win races and He build them every day for a living.
What are your folks thoughts on this?
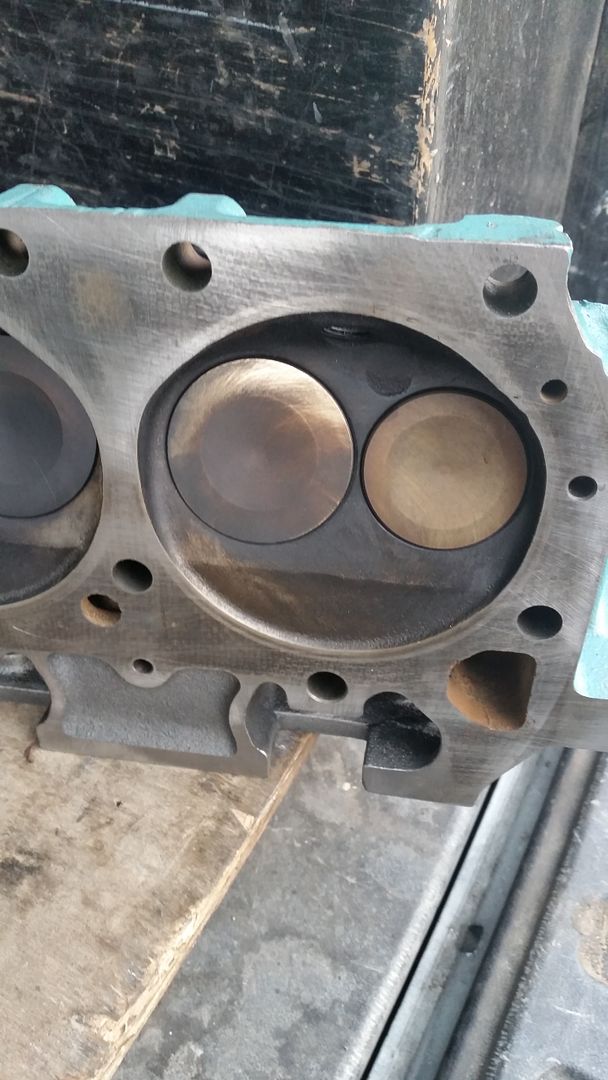
906 heads, 2.118 intake. I think thats what they mic out to. I will double check the size tomarrow.
He did say the exhaust valve size is fine.
Thanls again for the time and advice.