Well, here's something hopefully someone can chime in on. I have my U pipe in hand, and can already see why people jack the battery to the trunk when they do turbos - it's in the freaking way...
http://s43.photobucket.com/user/serj22/media/Turbo 225/IMG_20140824_182749_zpsc48252e2.jpg.html
Problem is - I want to leave the battery where it is - so I don't have to put a totally rad WW2 ammo box in the trunk for the battery to sit in. I really do like it where it is. And I know this can be done by leaving it there. So rather than having it front high, my new idea is to have it low, and centered. Basically the idea is to have the body floating right over the top of the steering box. There will be about 2" of clearance between them. I can raise the turbo itself higher, but I am worried about the leverage it will create on the bottom of the exhaust manifold.
This is an example of where it will go.
http://s43.photobucket.com/user/serj22/media/Turbo 225/IMG_20140824_184146_zpsd1e04994.jpg.html
It's resting on the steering box right now - but obviously it won't be and I will be dialing the oulet to face the other way to go to a 90* bend, towards the sky, then duck under the battery tray and then 90* into the intercooler. Then from intercooler, just pretty much like everyone else has up above the alternator bracket and into the carb.
SO this is my idea - scrapping the lengthened J pipe -
http://s43.photobucket.com/user/serj22/media/Turbo 225/IMG_20140824_184522_zps79472636.jpg.html
Just that (well the exhaust flange is angled a bit realistically, but you get the idea) - 1 1/2" apart and with the slightest U under it - basically the shortest thing allowing them to join, and possibly raising the turbo itself slightly by about 5". The throttle cable will still clear everything, and I'll be able to use the existing throttle and kickdown. The other awesome fact of this is the downpipe modification/ addition will be very short and will meet the original exhaust pretty spot-on, and leave the bung towards the firewall so that the wire can travel straight vertical - and into the cabin.
This also leaves HUGE amounts of room to run pretty much whatever intake piping I want, which will likely sweep up, and straight forward to keep it out of the muck if I accidentally drive through a lake.
The 5" rise on the U will allow my to tie the turbo to the same bolts that attach the intake and exhaust together by making a simple little bracket.
My question though - was I was originally going to go forward, and tie the turbo to where the A/C or power steering pump would go with a bracket off the block - which I assumed would support the weight.
My new idea allows it to mount to both manifolds, and utilize the same exhaust hanger bolted to the bellhousing near the back of the motor to hold the downpipe up. Will this be sufficient to support it and/or prevent cracking of the exhaust hopefully?
Also - intercooler update - took the car on freeway at 70 cruised for 20 mins, and only hit 190-195* so the intercooler is not blocking much. I'm assuming the car gets more airflow under the bumper and through the small slit above the license plate. One of the caps flew off the intercooler - looks like duct-tape for the time being.
It's invisible in certain lighting, but visible when you're right up next to the car.
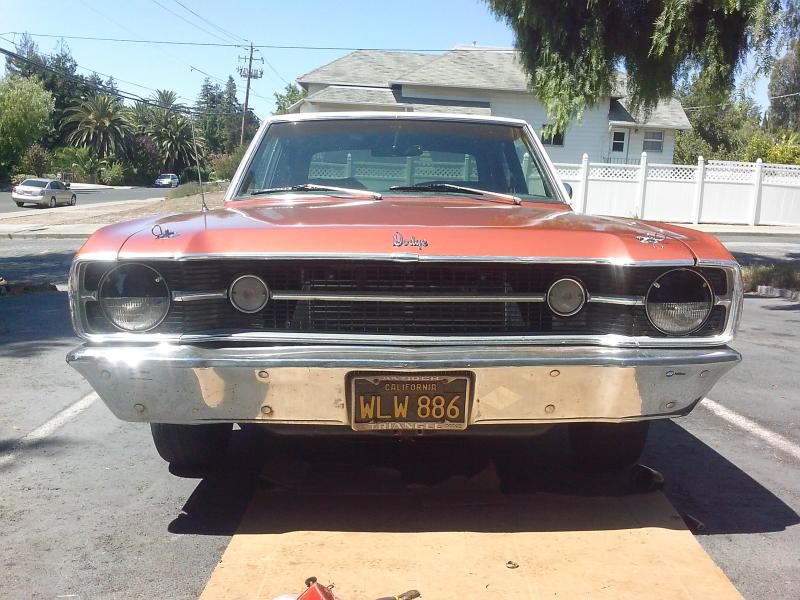