streetdak
Well-Known Member
So, I posted a help thread the other day when I found out my dipstick tube was cracked. Needless to say, I tried to remove it and it snapped like I had figured.
Well I've done this once before in my old 318, and I used the same method I did that time, with successful results. So I figured I should take a few pics and write up a lil tutorial on how I've been able to get it done for those in need.
Now I believe this will work the majority of the time, however I must say it may not work for everyone, and I think this will be most successful if you have not mangled or altered the remaining broken tube while attempting to remove it.
This write-up uses the Mechanical Fuel Pump as a Piviot. Please use caution, may not work for those with electrical fuel pumps, however may give some tips for those of you on a way to come up with your own tool.
First tip, remove the alternator and set it aside, reveling just the mechanical fuel pump with clear vision of where the dipstick tube enters the block.
You need to find either a long bolt or some all-thread (redfish suggested the all-thread so kudo's to him) that will basically fit in the remaining tube in the block. It has to fit tight enough that you can feel it start to thread with a 1/2 to 1 full turn of the bolt.
TIP, I used a stock battery hold down bolt, just happened to thread right in. It is about 8 or 9 inches long Not sure of the thread size, maybe someone can clear that up for me.
(Now if your going to use all-thread, make sure you use 2 nuts to "double nut" the all-thread to create a bolt head.)
Once you find the correct sized bolt or all thread, start threading the bolt into the broken tube with just about 2 or three turns. Then back the bolt out.
Slide 3 things over the bolt. This is what worked for me
1 Deep 18mm socket 3/8 drive
1 Regular 18mm socket 3/8 drive
1 5/8 closed end of a combination wrench.
These are going to create your leverage to remove the tube, so make sure they slide over the bolt but not over the head.
With all the "Spacers" slid over the bolt, carefully insert the bolt in the broken tube. Start the thread again, and then continue to thread the bolt into the tube until the wrench is lying on the upper neck of the mechanical Fuel Pump. Make sure the bolt threads nicely and doesn't strip, you should feel resistance when "tapping" the bolt. You should thread the bolt at least 3/4 of an inch in to the tube.
The wrench should be fairly taught as a pivot resting on the upper arm of the mechanical fuel pump.
Last step would be a simple couple wacks of the hammer on the end of the combination wrench while carefully keeping the combination wrench seated on the fuel pump arm.
It needs a decent initial whack to dislodge the tube but don't be a he man!
Once initially dislodged, a few taps will remove the remaining broken tube out of the block.
Good Luck, and take your time, any questions please ask, I know this may be a little confusing and i'll try to take some more pics of the process.
Well I've done this once before in my old 318, and I used the same method I did that time, with successful results. So I figured I should take a few pics and write up a lil tutorial on how I've been able to get it done for those in need.
Now I believe this will work the majority of the time, however I must say it may not work for everyone, and I think this will be most successful if you have not mangled or altered the remaining broken tube while attempting to remove it.
This write-up uses the Mechanical Fuel Pump as a Piviot. Please use caution, may not work for those with electrical fuel pumps, however may give some tips for those of you on a way to come up with your own tool.
First tip, remove the alternator and set it aside, reveling just the mechanical fuel pump with clear vision of where the dipstick tube enters the block.
You need to find either a long bolt or some all-thread (redfish suggested the all-thread so kudo's to him) that will basically fit in the remaining tube in the block. It has to fit tight enough that you can feel it start to thread with a 1/2 to 1 full turn of the bolt.
TIP, I used a stock battery hold down bolt, just happened to thread right in. It is about 8 or 9 inches long Not sure of the thread size, maybe someone can clear that up for me.
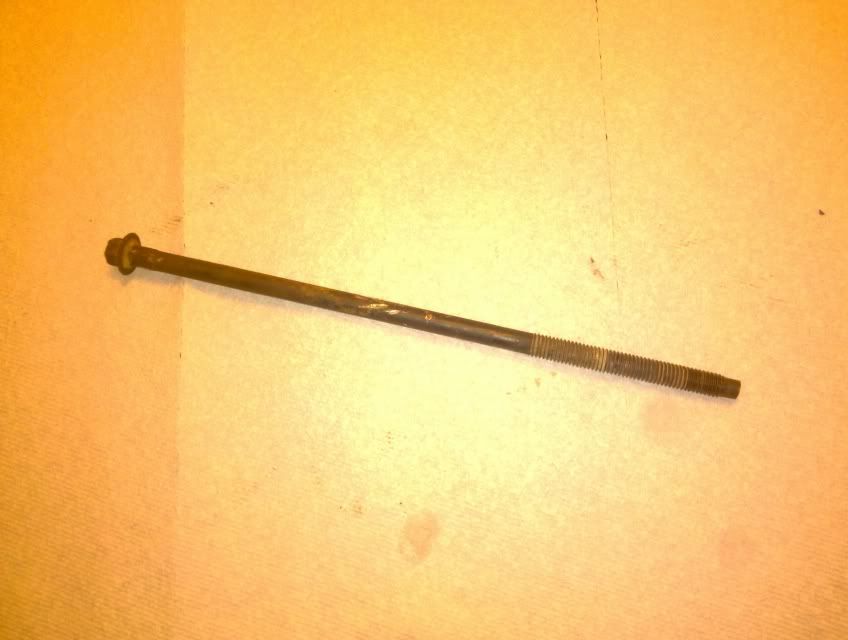
(Now if your going to use all-thread, make sure you use 2 nuts to "double nut" the all-thread to create a bolt head.)
Once you find the correct sized bolt or all thread, start threading the bolt into the broken tube with just about 2 or three turns. Then back the bolt out.
Slide 3 things over the bolt. This is what worked for me
1 Deep 18mm socket 3/8 drive
1 Regular 18mm socket 3/8 drive
1 5/8 closed end of a combination wrench.
These are going to create your leverage to remove the tube, so make sure they slide over the bolt but not over the head.
With all the "Spacers" slid over the bolt, carefully insert the bolt in the broken tube. Start the thread again, and then continue to thread the bolt into the tube until the wrench is lying on the upper neck of the mechanical Fuel Pump. Make sure the bolt threads nicely and doesn't strip, you should feel resistance when "tapping" the bolt. You should thread the bolt at least 3/4 of an inch in to the tube.
The wrench should be fairly taught as a pivot resting on the upper arm of the mechanical fuel pump.
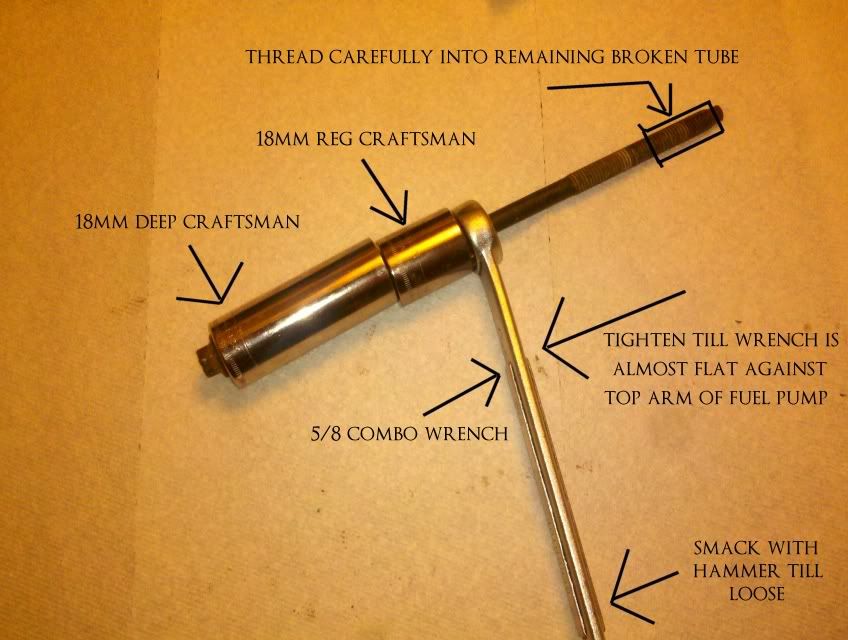
Last step would be a simple couple wacks of the hammer on the end of the combination wrench while carefully keeping the combination wrench seated on the fuel pump arm.
It needs a decent initial whack to dislodge the tube but don't be a he man!
Once initially dislodged, a few taps will remove the remaining broken tube out of the block.
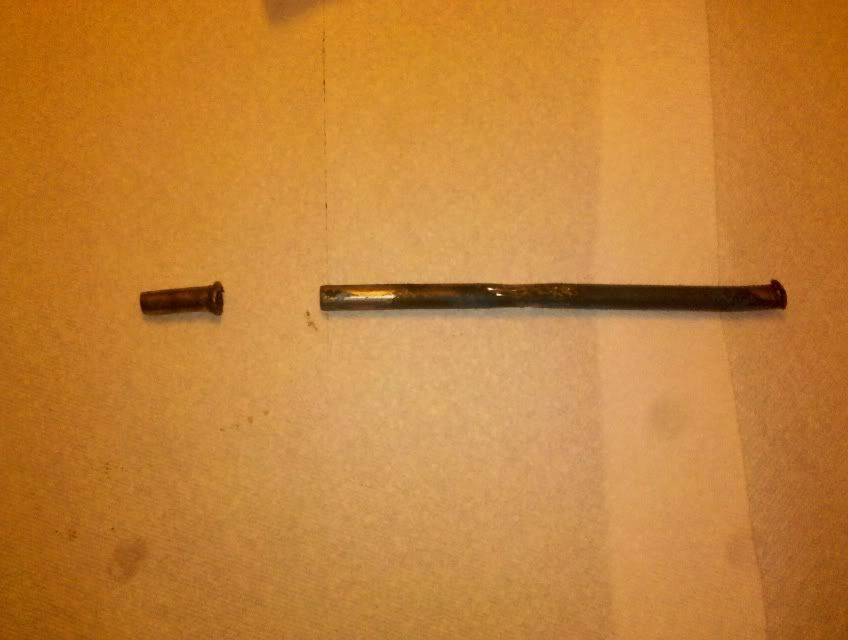
Good Luck, and take your time, any questions please ask, I know this may be a little confusing and i'll try to take some more pics of the process.