mattmatthew
^_^
I was a bit intimidated about posting in this section, as I'm definitely no expert on my own car. You won't see any gorgeous garages or work spaces here. I have a carport, and I work for the most part in the sun, the rain, etc. But I was really inspired by needsaresto's thread, so I'm posting this as a record of getting my car back on the road after sitting in the elements for almost 3 years.
So, some background on my car: I inherited it from my grandparents when they passed away, for the simple fact that no one wanted to drive it. My sister drove it briefly during college, and singlehandedly put every single dent in the car - not a big deal. For the most part, the body was straight and somewhat rust-free as it had been garaged for most of the 30-something years preceding me.
I still have the original documents from the car's purchase in West Lafayette, Indiana.
The check that paid for the car.
The original bill of lading and signed document from Matson to ship it to Hawaii. It cost a whopping $150 in 1965.
This is what she looked like in 2004.
In 2003, with DusterIdiot's help (slantsix.org) he pulled some parts for me - disc brake setup and LBP 7.25 rear end from a 76 Duster - from a wrecking yard in Salem, OR, crated it up and had it shipped to me in Hawaii. Hawaii doesn't have a TON of mopars or a ton of wrecking yards. In fact, the last real yard where you could pull parts on your own closed mid 2006 - a shame really, but before they closed I scored a set of LBP 14" wheels. With the help of my friend Bob, we put in the rear end, but the disc setup we never got to as work, money, and other more immediate issues with the car got in the way.
Around 2006, my friend Bob helped me fix a persistent oil leak. After pulling the oil pan and changing the gasket multiple times - we finally figured out it was leaking at the rear crankshaft bearing. The bottom gasket was pretty much shot, so we yanked the motor, changed out the gasket with a new rubber one.
And got everything painted.
Meet Bob.
Since we had the engine out, we decided to hook up the Super Six manifold and the throttle linkage and kickdown setup that came off a local 63 Valiant.
We also converted the distributor to electronic ignition and dropped a nice MSD box and coil in there.
Test drive time!
So, some background on my car: I inherited it from my grandparents when they passed away, for the simple fact that no one wanted to drive it. My sister drove it briefly during college, and singlehandedly put every single dent in the car - not a big deal. For the most part, the body was straight and somewhat rust-free as it had been garaged for most of the 30-something years preceding me.
I still have the original documents from the car's purchase in West Lafayette, Indiana.
The check that paid for the car.
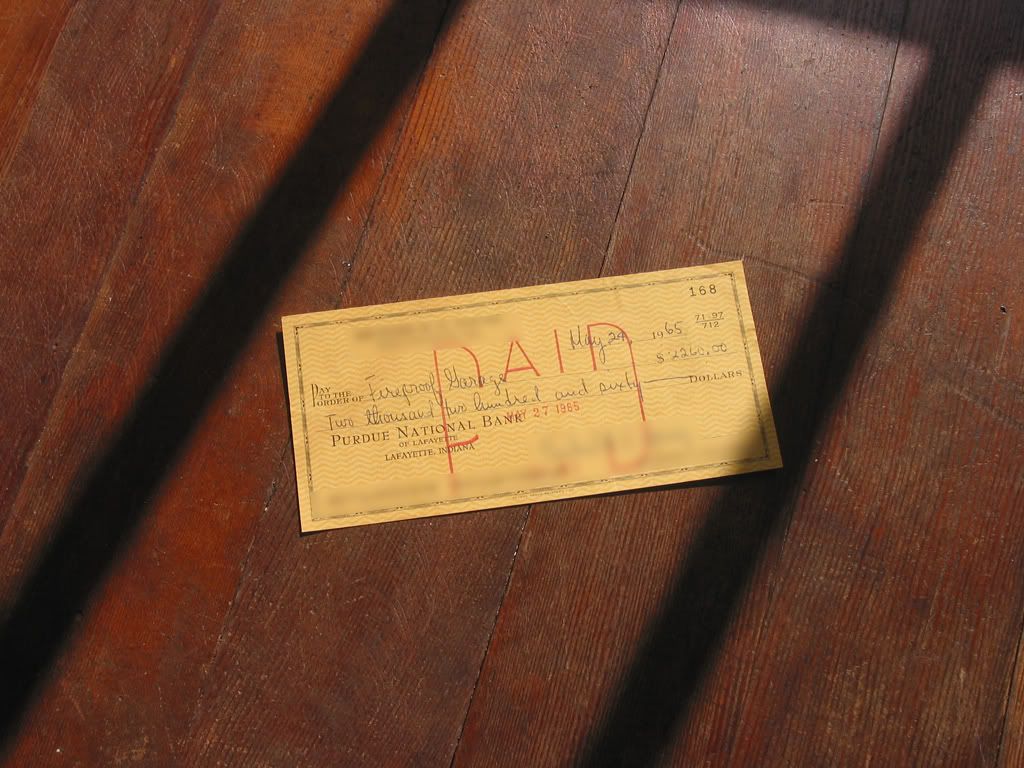
The original bill of lading and signed document from Matson to ship it to Hawaii. It cost a whopping $150 in 1965.
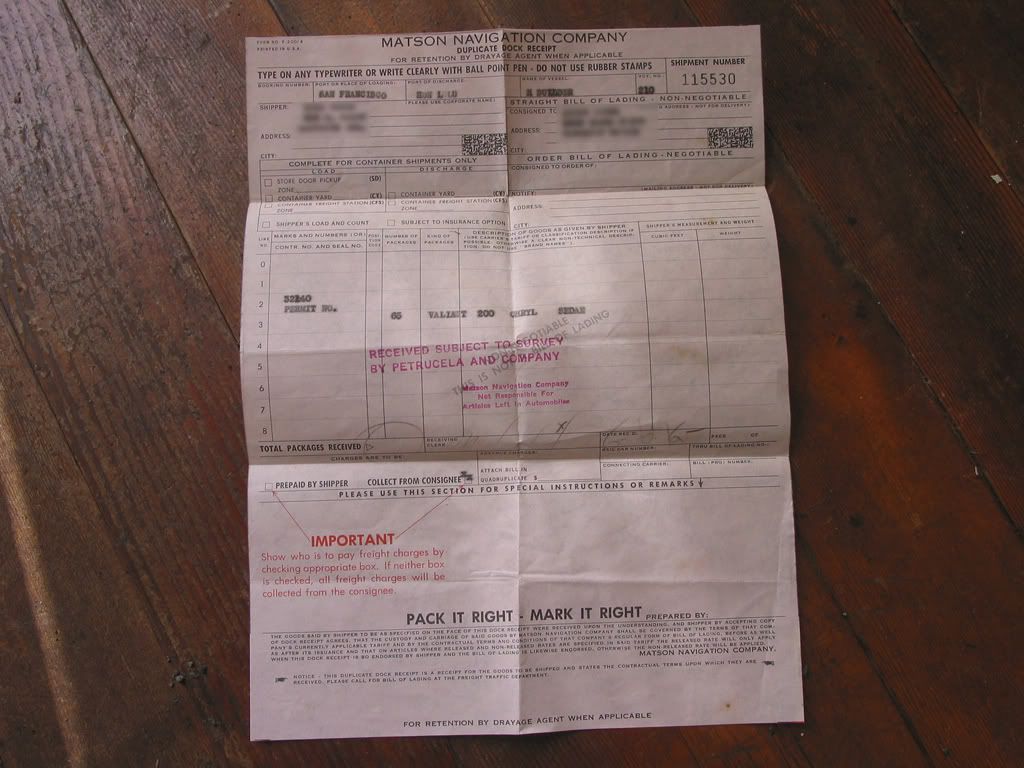
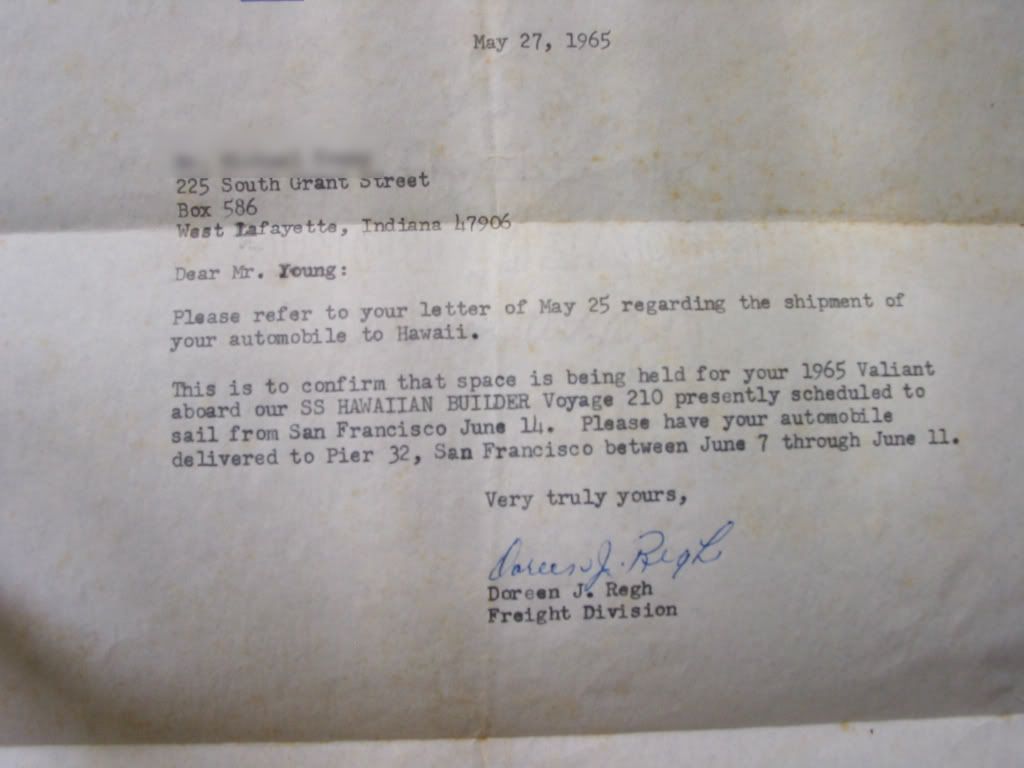
This is what she looked like in 2004.
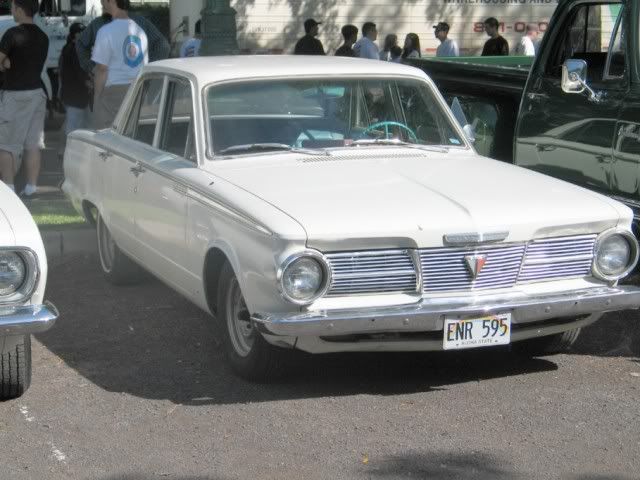
In 2003, with DusterIdiot's help (slantsix.org) he pulled some parts for me - disc brake setup and LBP 7.25 rear end from a 76 Duster - from a wrecking yard in Salem, OR, crated it up and had it shipped to me in Hawaii. Hawaii doesn't have a TON of mopars or a ton of wrecking yards. In fact, the last real yard where you could pull parts on your own closed mid 2006 - a shame really, but before they closed I scored a set of LBP 14" wheels. With the help of my friend Bob, we put in the rear end, but the disc setup we never got to as work, money, and other more immediate issues with the car got in the way.
Around 2006, my friend Bob helped me fix a persistent oil leak. After pulling the oil pan and changing the gasket multiple times - we finally figured out it was leaking at the rear crankshaft bearing. The bottom gasket was pretty much shot, so we yanked the motor, changed out the gasket with a new rubber one.
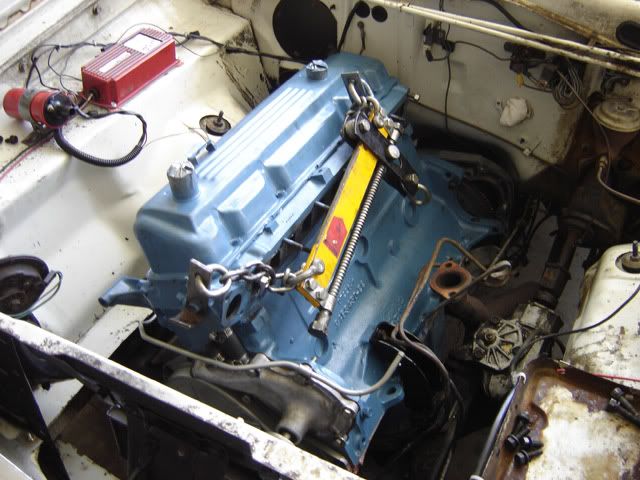
And got everything painted.
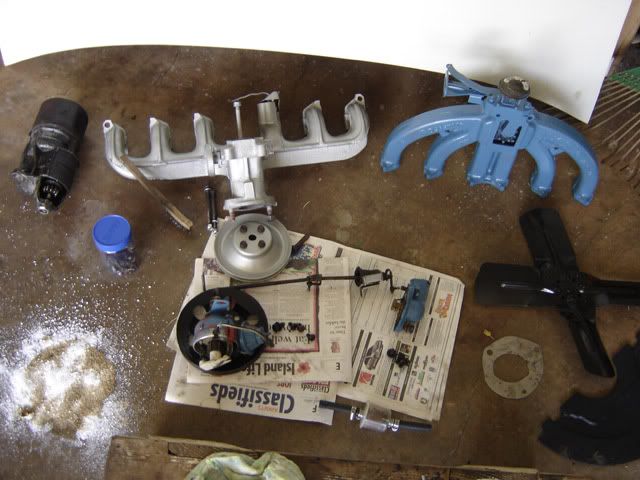
Meet Bob.
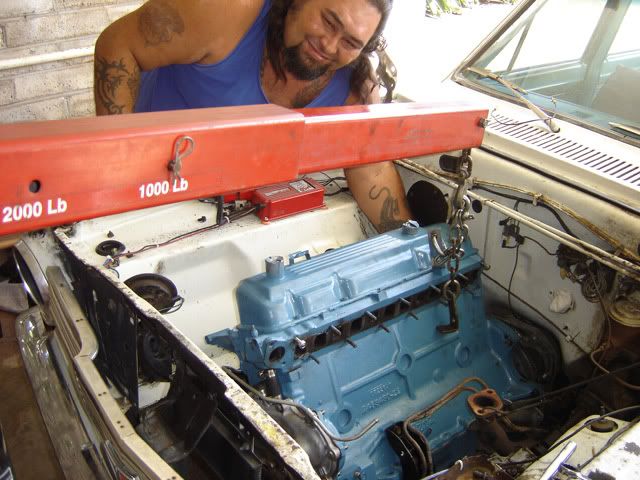
Since we had the engine out, we decided to hook up the Super Six manifold and the throttle linkage and kickdown setup that came off a local 63 Valiant.
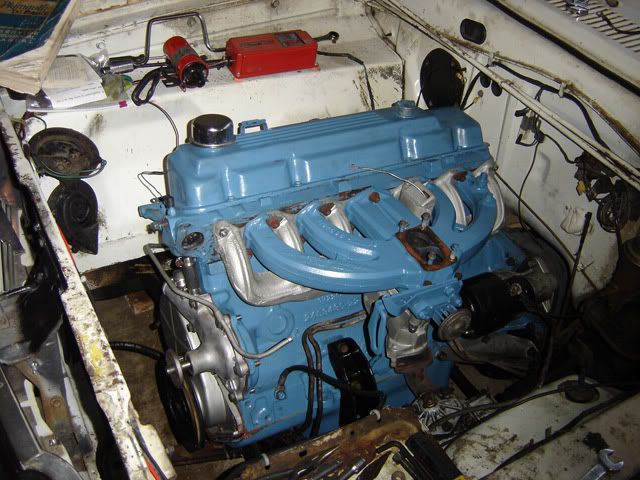
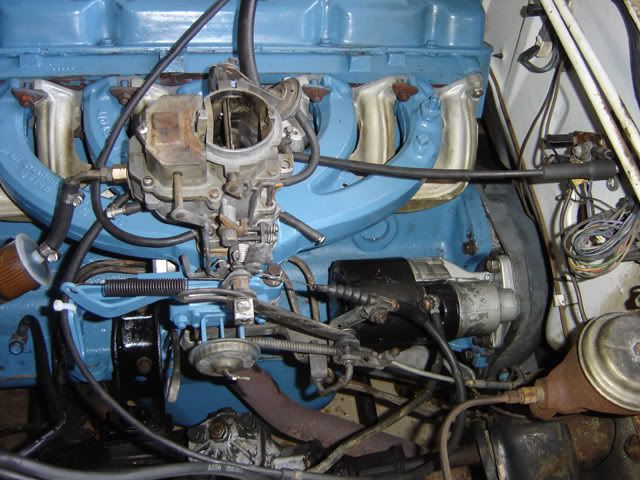
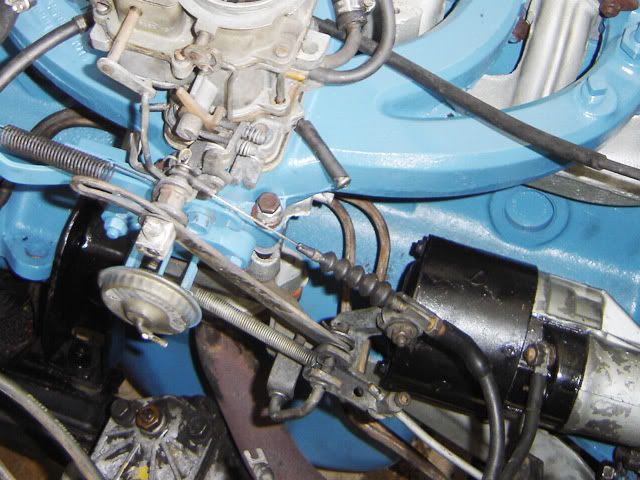
We also converted the distributor to electronic ignition and dropped a nice MSD box and coil in there.
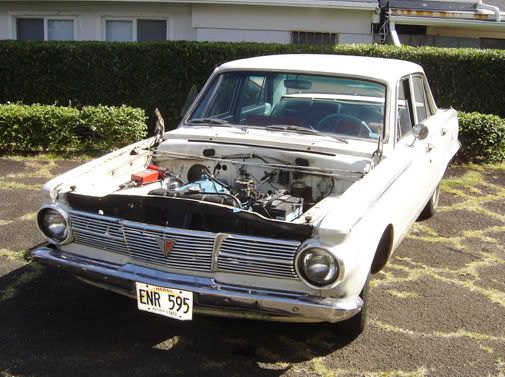
Test drive time!