ardentindustries
Well-Known Member
Hey all,
Its a well known fact that the front of our cars SUCK when it comes to rigidity and structural integrity. This becomes a much bigger problem when you start cutting corners as one can imagine.
I have had this idea for awhile now, and finally was able to bend up a piece today. The rear mounts to the front of the subframe connector, while the front mounts to the outside of the front subframe rail. Of course, in the mount areas, a plate would be welded first, and then the tube to the plate.
This is about as tight to the factory body structure as can be, so hopefully it doesnt get in the way of bigger tires. It would definitely be okay with stock size tires. This, together with subframe connectors(coming soon...), and I think you are about as close to a full tube frame as you can be without actually have a tube frame...if that makes sense.
For install, a hole would need to be drilled in the vertical sheetmetal panel behind the wheel opening, and a portion of the factory "gusset" for the shock mount needs to be removed. Both take less than 10 minutes per side.
This is just an idea...looking for input. Just thought Id throw it out there. It'll take some fabrication work, but Im not a fan of bolt on stuff. Let me know what you think. Thanks.
Its dark here now, so nevermind the "flash" pictures.
Its a well known fact that the front of our cars SUCK when it comes to rigidity and structural integrity. This becomes a much bigger problem when you start cutting corners as one can imagine.
I have had this idea for awhile now, and finally was able to bend up a piece today. The rear mounts to the front of the subframe connector, while the front mounts to the outside of the front subframe rail. Of course, in the mount areas, a plate would be welded first, and then the tube to the plate.
This is about as tight to the factory body structure as can be, so hopefully it doesnt get in the way of bigger tires. It would definitely be okay with stock size tires. This, together with subframe connectors(coming soon...), and I think you are about as close to a full tube frame as you can be without actually have a tube frame...if that makes sense.
For install, a hole would need to be drilled in the vertical sheetmetal panel behind the wheel opening, and a portion of the factory "gusset" for the shock mount needs to be removed. Both take less than 10 minutes per side.
This is just an idea...looking for input. Just thought Id throw it out there. It'll take some fabrication work, but Im not a fan of bolt on stuff. Let me know what you think. Thanks.
Its dark here now, so nevermind the "flash" pictures.
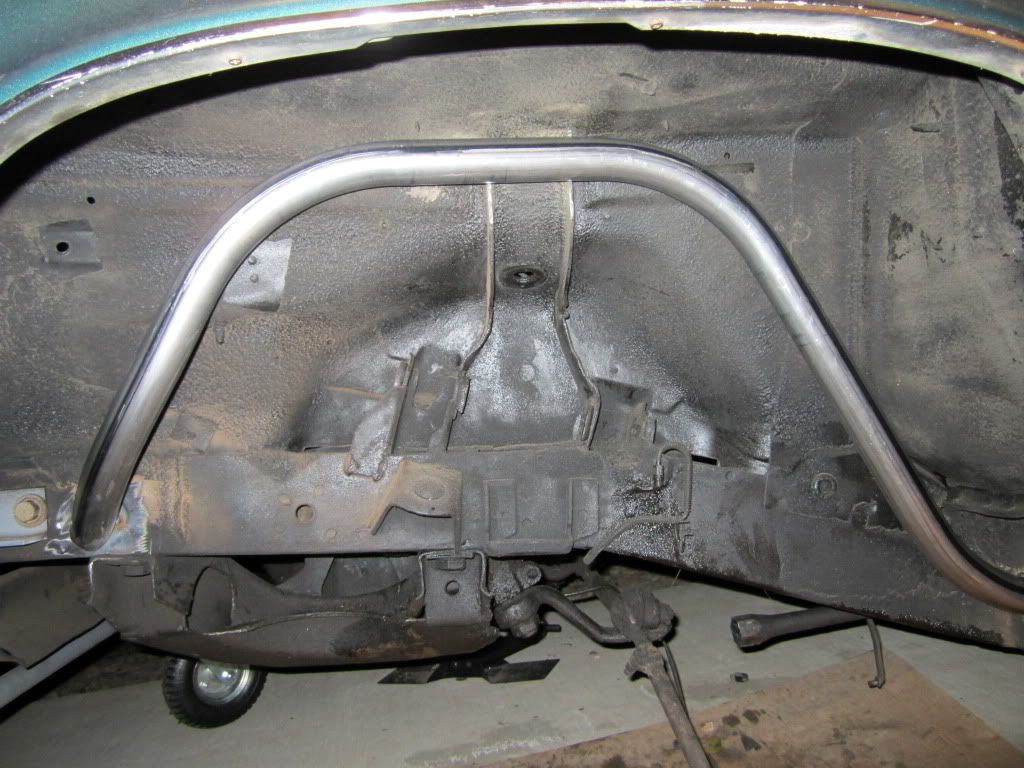
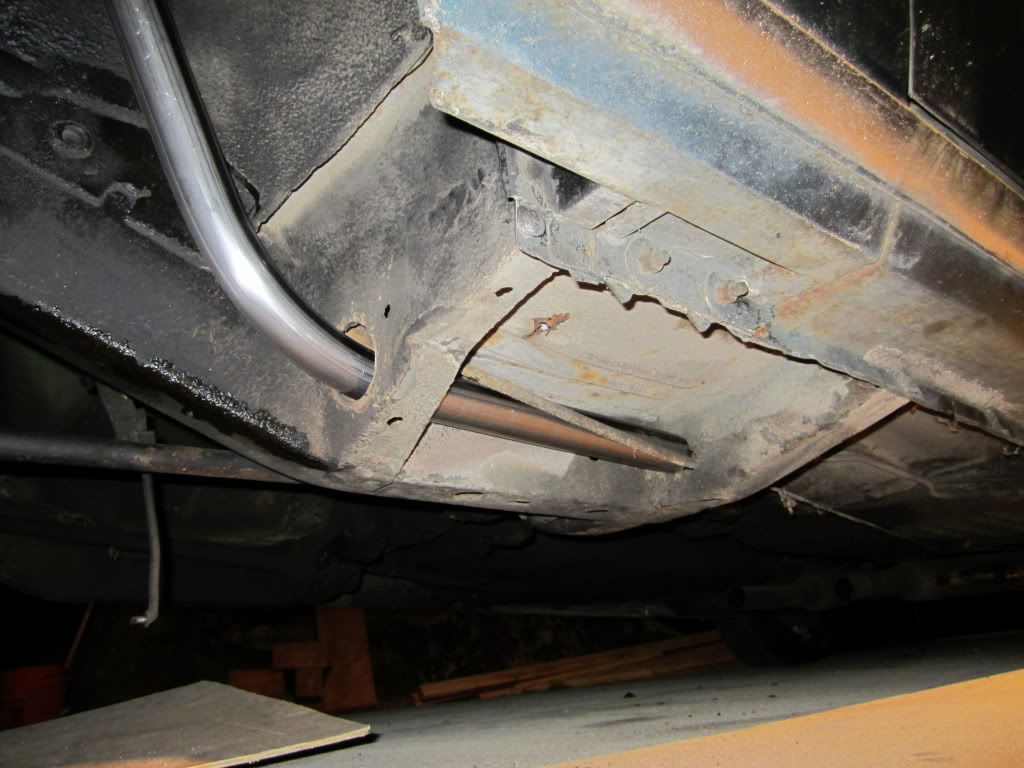
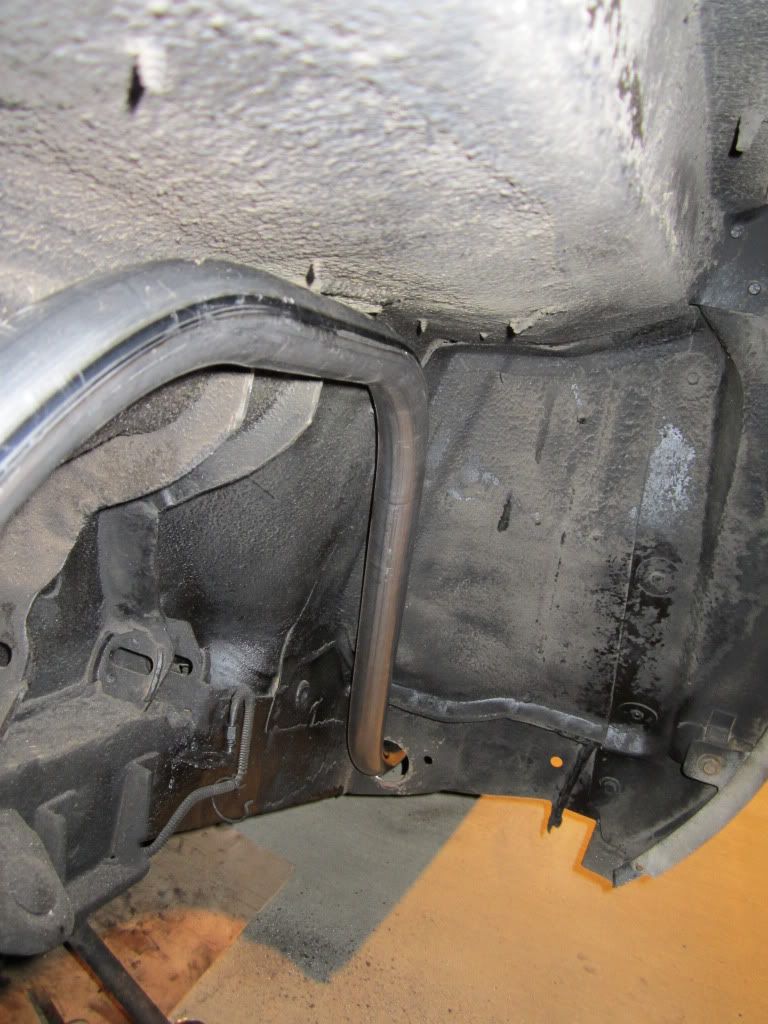
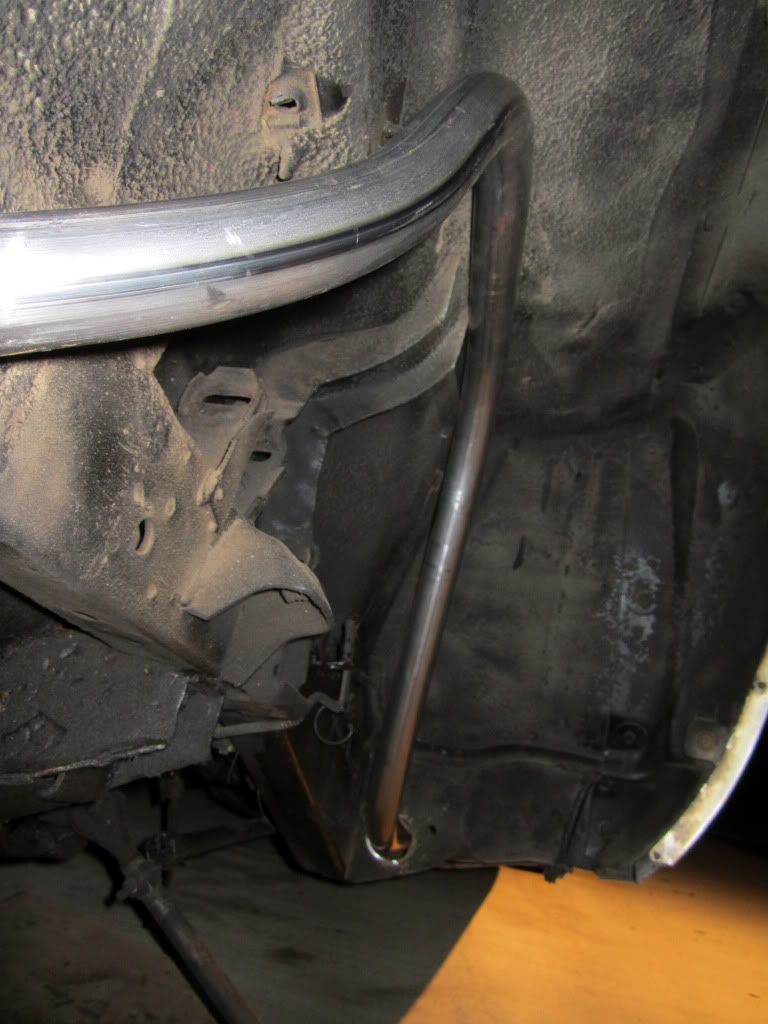
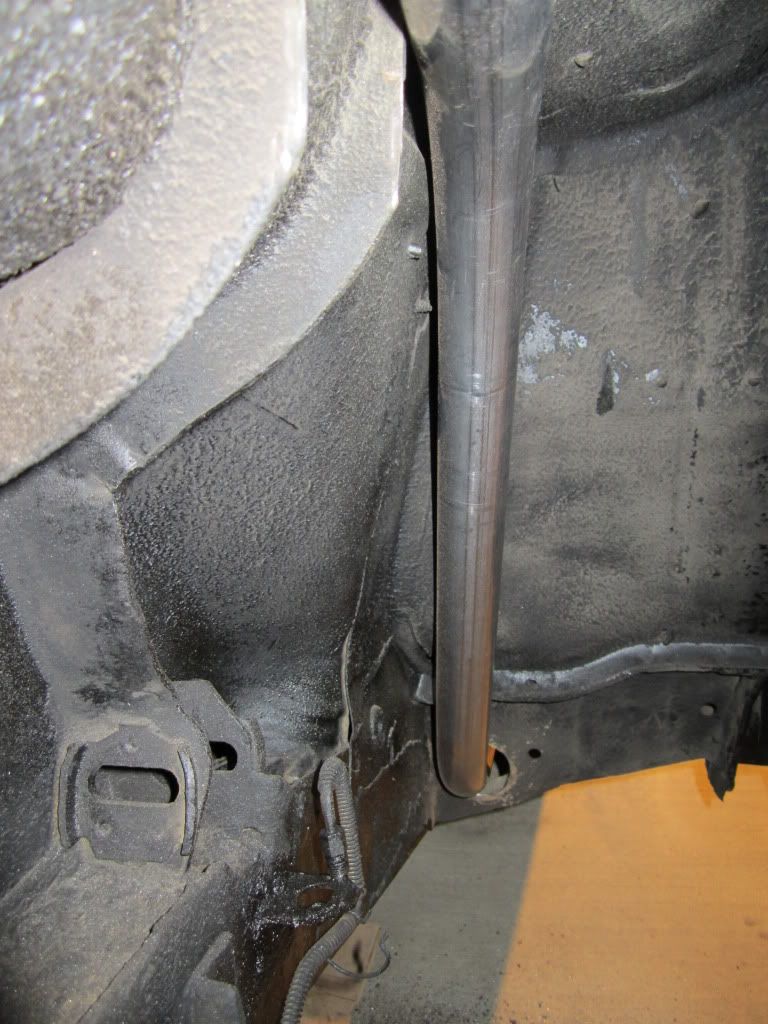